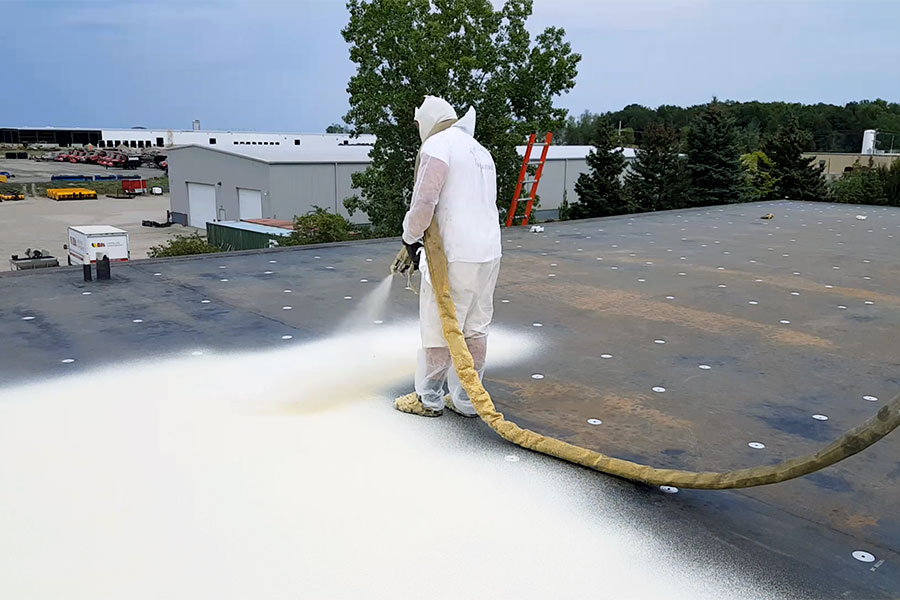
What is Spray Foam Roofing and Why Choose It?
Spray foam roofing represents one of the most innovative and effective commercial roofing solutions available today. This advanced roofing system involves applying a liquid mixture of polyol resin and isocyanate that expands into a solid foam when sprayed onto the roof surface. The result is a seamless, monolithic membrane that provides exceptional insulation, waterproofing, and structural integrity for commercial buildings.
The spray foam roofing system has gained tremendous popularity among commercial property owners due to its unique ability to address multiple roofing challenges simultaneously. Unlike traditional roofing materials that require seams, joints, and mechanical fasteners, spray foam creates a continuous barrier that eliminates common leak points. This seamless application makes it particularly valuable for buildings with complex roof geometries, including those with skylights, HVAC equipment, and irregular shapes.
Modern spray foam roofing technology has evolved significantly over the past decade, with manufacturers developing formulations that offer enhanced durability, better adhesion, and improved weather resistance. The system typically consists of two main components: the spray foam insulation layer and a protective coating system that shields the foam from UV radiation and weather elements.
How Spray Foam Roofing Systems Work
The science behind spray foam roofing lies in its unique chemical composition and application process. When the two liquid components are mixed and sprayed, they undergo a rapid chemical reaction that causes the mixture to expand up to 30 times its original volume. This expansion allows the foam to fill every crack, crevice, and irregular surface, creating a perfect seal that traditional roofing materials cannot achieve.
The cellular structure of cured spray foam consists of millions of tiny bubbles that trap air, providing exceptional thermal insulation properties. This structure gives spray foam roofing an R-value of approximately 6.5 per inch of thickness, making it one of the most efficient insulation materials available. The closed-cell structure also prevents water infiltration, making the system inherently waterproof.
The application process requires skilled technicians who use specialized equipment to maintain proper mixing ratios and application temperatures. The foam is typically applied in multiple passes, with each lift being approximately 1-2 inches thick. This controlled application ensures proper adhesion and allows for precise thickness control across the entire roof surface.
Types of Spray Foam Roofing Materials
Closed-Cell Spray Foam
Closed-cell spray foam roofing offers the highest performance characteristics and is the most commonly used type for commercial applications. This material features a dense cellular structure where individual cells are completely sealed, preventing air and moisture penetration. The density typically ranges from 2 to 3 pounds per cubic foot, providing excellent structural strength and dimensional stability.
The closed-cell structure provides superior insulation properties, with thermal resistance values that remain consistent over time. This type of spray foam roofing also offers excellent adhesion to various substrates, including concrete, metal, and existing roofing materials. The material’s low permeability makes it ideal for applications where moisture control is critical.
Open-Cell Spray Foam
Open-cell spray foam roofing features a lighter density structure, typically around 0.5 pounds per cubic foot, with interconnected cells that allow some air movement. While less commonly used for primary roofing applications, open-cell foam can be beneficial in specific situations where vapor permeability is desired or where cost considerations are paramount.
The open-cell structure provides good insulation properties while allowing the material to remain flexible. This flexibility can be advantageous in applications where building movement is expected. However, open-cell spray foam requires additional vapor barriers in most commercial roofing applications.
Installation Process for Spray Foam Roofing
The installation of a spray foam roofing system requires careful planning and execution to ensure optimal performance. The process begins with a thorough inspection and preparation of the existing roof substrate. All loose materials, debris, and contaminants must be removed, and any necessary repairs to the deck structure must be completed before foam application.
Surface preparation is critical for proper adhesion and long-term performance. The substrate must be clean, dry, and free from oils, dust, or other substances that could interfere with bonding. Depending on the existing roof condition, this may involve power washing, scraping, or chemical cleaning. All penetrations, drains, and roof equipment must be properly detailed and protected during the installation process.
Weather conditions play a crucial role in spray foam application. The installation must occur when ambient temperatures are between 40°F and 100°F, with humidity levels below 85%. Wind conditions must also be considered, as excessive wind can affect the spray pattern and foam quality. Professional installers use specialized equipment that maintains precise temperature and pressure controls to ensure consistent foam quality.
The foam application process typically involves multiple passes to achieve the desired thickness. Each pass must be properly timed to ensure good adhesion between layers while preventing over-application that could lead to surface defects. The installer must maintain consistent spray patterns and thickness to create a uniform surface that will accept the protective coating system.
Benefits of Spray Foam Roofing for Commercial Buildings
Superior Energy Efficiency
Spray foam roofing delivers exceptional energy efficiency benefits that can significantly reduce building operating costs. The high R-value insulation properties combined with the seamless application create a thermal barrier that eliminates common thermal bridges found in traditional roofing systems. This enhanced insulation performance can reduce heating and cooling costs by 20-50% compared to conventional roofing systems.
The air sealing properties of spray foam roofing also contribute to energy savings by preventing conditioned air from escaping through roof penetrations and seams. This improved building envelope performance reduces the load on HVAC systems and can extend equipment life by reducing operating cycles. Many commercial buildings with spray foam roofing systems report improved indoor comfort and more consistent temperatures throughout the building.
Exceptional Durability and Longevity
The monolithic nature of spray foam roofing systems provides exceptional durability and weather resistance. Unlike traditional roofing materials that deteriorate at seams and mechanical fasteners, spray foam creates a continuous membrane that maintains its integrity over time. Properly installed and maintained spray foam roofing systems can last 20-30 years or more, making them a cost-effective long-term investment.
The foam’s ability to expand and contract with temperature changes without losing adhesion prevents the stress failures common in other roofing materials. This flexibility, combined with the material’s inherent waterproofing properties, provides reliable protection against water infiltration even in extreme weather conditions.
Versatility and Adaptability
Spray foam roofing systems offer unmatched versatility for commercial applications. The material can be applied to virtually any roof substrate, including concrete, metal, wood, and existing roofing materials. This adaptability makes spray foam roofing an excellent choice for retrofit applications where removing existing roofing would be costly or disruptive.
The system’s ability to conform to complex roof geometries makes it ideal for buildings with multiple roof levels, skylights, HVAC equipment, and other penetrations. The seamless application eliminates the need for complex flashing details and reduces potential leak points that are common with traditional roofing systems.
Cost Analysis of Spray Foam Roofing
The initial cost of spray foam roofing installation typically ranges from $4.50 to $8.50 per square foot, depending on various factors including roof complexity, thickness requirements, and regional labor costs. While this initial investment may be higher than some traditional roofing materials, the long-term value proposition makes spray foam roofing an attractive option for commercial building owners.
The cost analysis must consider the total cost of ownership, including installation, maintenance, energy savings, and system longevity. When spray foam cost factors are evaluated over the system’s expected lifespan, the cost per year of service often compares favorably to traditional roofing systems that require more frequent replacement and maintenance.
Energy savings represent a significant component of the spray foam roofing value proposition. Buildings with spray foam roofing systems typically experience reduced energy consumption that can offset the initial cost premium within 5-10 years. These savings continue throughout the system’s life, providing ongoing value that improves the return on investment.
Maintenance Requirements for Spray Foam Roofing
Spray foam roofing systems require minimal maintenance compared to traditional roofing materials, but regular inspections and preventive care are essential for optimal performance. The maintenance program should include bi-annual inspections to identify any potential issues before they become significant problems. These inspections should focus on the protective coating system, drainage areas, and roof penetrations.
The protective coating system requires periodic renewal to maintain UV protection and weather resistance. Depending on the coating type and environmental conditions, recoating may be necessary every 10-15 years. This maintenance requirement is significantly less frequent than the repairs and replacements typically required for traditional roofing systems.
Routine maintenance tasks include keeping the roof surface clean of debris, ensuring proper drainage, and promptly addressing any mechanical damage. The seamless nature of spray foam roofing makes repair work straightforward, as damaged areas can be easily accessed and repaired without affecting the surrounding roof membrane.
Environmental Impact and Sustainability
The environmental benefits of spray foam roofing extend beyond energy efficiency to include reduced material waste and improved building sustainability. The system’s longevity reduces the frequency of roof replacements, minimizing construction waste and resource consumption over time. The energy efficiency benefits also contribute to reduced carbon emissions from building operations.
Modern spray foam formulations have evolved to include more environmentally friendly blowing agents and reduced volatile organic compound (VOC) emissions. Many manufacturers have developed products that meet or exceed environmental standards while maintaining performance characteristics. The recyclability of spray foam materials at the end of their service life further enhances the environmental profile of these systems.
The cool roof properties of spray foam roofing with reflective coatings can help reduce the urban heat island effect in metropolitan areas. This environmental benefit extends beyond the individual building to contribute to improved local air quality and reduced energy demand across the urban environment.
Common Applications and Building Types
Commercial and Industrial Buildings
Spray foam roofing is particularly well-suited for large commercial and industrial buildings where energy efficiency and long-term performance are priorities. Manufacturing facilities, warehouses, and distribution centers benefit from the system’s ability to provide superior insulation and air sealing across large roof areas. The seamless application is especially valuable in buildings with complex roof geometries and multiple penetrations.
Retail buildings and shopping centers represent another major application area for spray foam roofing systems. These buildings often have complex roof configurations with multiple levels, skylights, and HVAC equipment that make traditional roofing systems challenging to install and maintain. The adaptability of spray foam roofing makes it an ideal solution for these applications.
Institutional Buildings
Schools, hospitals, and government buildings often choose spray foam roofing for its energy efficiency and long-term durability. These institutional applications value the system’s ability to provide consistent performance over extended periods while minimizing maintenance requirements. The improved indoor air quality and comfort benefits are particularly important in these occupied spaces.
The fire resistance properties of spray foam roofing systems make them suitable for applications where building safety is a primary concern. When properly installed with appropriate fire-rated coatings, spray foam roofing can meet or exceed fire safety requirements for commercial buildings.
Quality Control and Installation Standards
The success of any spray foam roofing installation depends on strict adherence to quality control procedures and industry standards. Professional installers must be trained and certified in spray foam application techniques, equipment operation, and safety procedures. The Spray Polyurethane Foam Alliance (SPFA) provides comprehensive training and certification programs for installers.
Quality control begins with proper material handling and storage. Both foam components must be stored at appropriate temperatures and protected from moisture contamination. The mixing and application equipment must be properly calibrated and maintained to ensure consistent foam quality throughout the installation process.
Installation standards require specific procedures for surface preparation, foam application, and coating installation. These standards address thickness requirements, surface preparation criteria, and environmental conditions for application. Adherence to these standards is essential for warranty coverage and long-term system performance.
Technology Advances in Spray Foam Roofing
Recent technological advances have significantly improved the performance and application characteristics of spray foam roofing systems. New formulations offer enhanced adhesion properties, improved weather resistance, and faster cure times that increase installation efficiency. These improvements have made spray foam roofing more versatile and reliable for a wider range of commercial applications.
Equipment advances have also contributed to improved installation quality and efficiency. Modern spray foam equipment features better temperature and pressure controls, improved mixing systems, and enhanced application tools that provide more consistent results. These technological improvements have reduced installation variables and improved overall system quality.
Smart coating technologies are emerging that can provide additional functionality beyond traditional protective coatings. These advanced coatings may include self-healing properties, enhanced reflectivity, or integrated monitoring capabilities that provide real-time feedback on system performance.
Take Action: Protect Your Commercial Building with Spray Foam Roofing
Don’t let your commercial building suffer from energy losses, frequent repairs, and costly maintenance associated with traditional roofing systems. Spray foam roofing offers the superior protection, energy efficiency, and long-term value your building needs. Contact a certified spray foam roofing contractor today to schedule a comprehensive roof assessment and discover how this innovative roofing solution can transform your building’s performance.
The investment in spray foam roofing pays dividends through reduced energy costs, minimal maintenance requirements, and extended roof life. Take the first step toward better building protection by consulting with spray foam roofing professionals who can evaluate your specific needs and provide customized solutions.
Frequently Asked Questions About Spray Foam Roofing
Q: How long does spray foam roofing last? A: Properly installed spray foam roofing systems typically last 20-30 years or more with appropriate maintenance. The seamless membrane and protective coating system provide exceptional durability and weather resistance that exceeds most traditional roofing materials.
Q: Is spray foam roofing suitable for all commercial building types? A: Spray foam roofing is suitable for most commercial building types, including warehouses, manufacturing facilities, retail buildings, and institutional structures. The system’s versatility allows it to be applied to various substrates and roof configurations.
Q: What maintenance is required for spray foam roofing? A: Spray foam roofing requires minimal maintenance, including bi-annual inspections, keeping the roof clean of debris, and periodic recoating of the protective coating system every 10-15 years. This maintenance schedule is significantly less intensive than traditional roofing systems.
Q: How does spray foam roofing perform in extreme weather conditions? A: Spray foam roofing performs exceptionally well in extreme weather conditions due to its seamless membrane and flexible properties. The system can withstand temperature extremes, high winds, and severe weather without compromising its integrity or waterproofing capabilities.
Q: Can spray foam roofing be installed over existing roofing materials? A: Yes, spray foam roofing can often be installed over existing roofing materials, making it an excellent retrofit solution. This capability reduces installation costs and waste while providing superior performance over the existing system.
Q: What is the R-value of spray foam roofing? A: Spray foam roofing typically provides an R-value of approximately 6.5 per inch of thickness, making it one of the most efficient insulation materials available. This high thermal resistance contributes to significant energy savings in commercial buildings.
Q: How quickly can spray foam roofing be installed? A: Installation speed depends on roof size and complexity, but spray foam roofing can typically be installed more quickly than traditional roofing systems. The seamless application eliminates the need for complex flashing details and reduces installation time.
Q: Does spray foam roofing require special equipment for installation? A: Yes, spray foam roofing requires specialized equipment for mixing and application. Professional installers use temperature-controlled spray equipment that maintains precise mixing ratios and application parameters to ensure consistent foam quality.