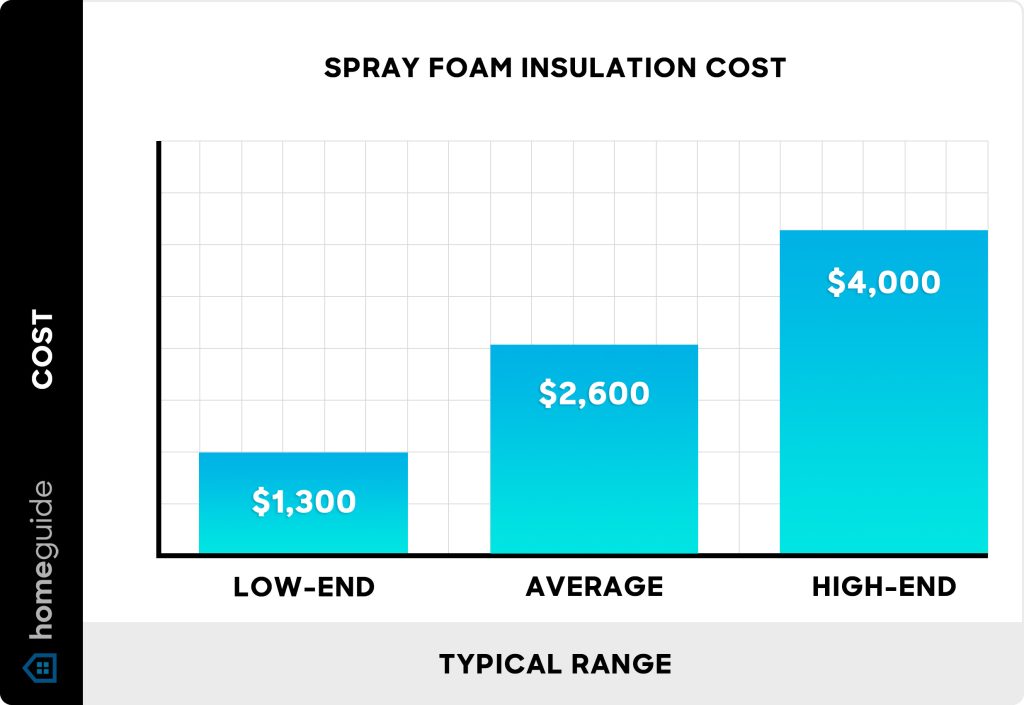
Understanding the spray foam insulation cost per square foot is crucial for homeowners planning energy-efficient upgrades. With rising energy costs and increasing focus on sustainable home improvements, spray foam insulation has become a popular choice for its superior thermal performance and air sealing capabilities. This comprehensive analysis will break down everything you need to know about spray foam insulation pricing, helping you make informed decisions for your home improvement project.
Current Spray Foam Insulation Cost Per Square Foot in 2025
The spray foam insulation cost per square foot varies significantly based on several factors, with current market prices ranging from $1.00 to $4.50 per square foot for professional installation. This wide price range reflects the different types of spray foam available, application methods, and regional labor costs across the United States.
Open-cell spray foam typically costs between $1 to $3 per square foot, while closed-cell foam commands a premium price of $1.50 to $4 per square foot. The higher cost of closed-cell foam is justified by its superior R-value, moisture resistance, and structural reinforcement properties. For a typical 2,000-square-foot home, homeowners can expect to invest anywhere from $2,000 to $8,000 depending on the foam type and thickness requirements.
Labor costs represent a significant portion of the total spray foam insulation expense. Professional contractors typically charge $0.44 to $3.30 per square foot for labor, though some contractors prefer hourly rates ranging from $50 to $100 per hour. The complexity of the installation area, accessibility challenges, and local market conditions all influence these labor rates.
Open-Cell vs Closed-Cell Spray Foam Pricing Analysis
Open-Cell Spray Foam Cost Breakdown
Open-cell spray foam, also known as half-pound foam due to its density of approximately 0.5 pounds per cubic foot, represents the more budget-friendly option for homeowners. The material cost for open-cell foam ranges from $0.45 to $0.75 per board foot, making it an attractive choice for large-area applications like attics and wall cavities.
The lower density of open-cell foam means it requires more material to achieve the same R-value as closed-cell foam, but its excellent sound-dampening properties and breathability make it ideal for interior applications. Open-cell foam typically achieves an R-value of approximately 3.5 to 4 per inch, requiring greater thickness to meet building code requirements in colder climates.
Closed-Cell Spray Foam Investment
Closed-cell spray foam commands higher prices due to its superior performance characteristics. At approximately 2 pounds per cubic foot density, closed-cell foam costs $1.00 to $1.60 per board foot for materials alone. The R-value is roughly 6.5 per inch, making it more efficient at providing thermal resistance with less thickness.
The premium pricing of closed-cell foam reflects its multiple benefits beyond insulation. This foam type provides structural reinforcement, acts as a vapor barrier, and offers excellent moisture resistance. These properties make closed-cell foam particularly valuable in basements, crawl spaces, and exterior applications where moisture control is critical.
Regional Variations in Spray Foam Insulation Cost
Geographic location significantly impacts spray foam insulation cost per square foot due to variations in labor costs, material transportation expenses, and local building codes. Metropolitan areas typically see higher installation costs due to increased labor rates and operational expenses, while rural areas may face higher material costs due to transportation logistics.
Northern climates often require thicker insulation applications to meet energy codes, increasing the overall project cost. Conversely, southern regions may achieve code compliance with thinner applications, reducing material usage and labor time. Regional competition among contractors also influences pricing, with areas having more spray foam specialists typically offering more competitive rates.
Building permit requirements vary by location and can add $50 to $200 to project costs. Some municipalities require additional inspections for spray foam installations, particularly in new construction or major renovation projects. These regulatory factors should be considered when budgeting for spray foam insulation projects.
Project Size Impact on Cost Per Square Foot
The scale of your spray foam insulation project significantly affects the cost per square foot, with larger projects typically achieving better economies of scale. Small projects under 500 square feet often face higher per-square-foot costs due to minimum service charges and equipment setup fees. Contractors may charge premium rates for small jobs to cover their operational costs and time investment.
Medium-sized projects between 500 and 2,000 square feet typically see the most competitive pricing as they provide contractors with reasonable profit margins while maintaining efficiency. Large-scale projects exceeding 2,000 square feet often qualify for volume discounts, though complex geometries or difficult access areas can offset these savings.
For a 1,500-square-foot home, expect total costs ranging from $1,500 to $7,500 including both materials and labor. This wide range reflects the variables affecting spray foam pricing and emphasizes the importance of obtaining multiple quotes for accurate project budgeting.
DIY vs Professional Installation Cost Comparison
DIY Spray Foam Kits Pricing
DIY spray foam insulation kits offer significant cost savings for smaller projects and handy homeowners. DIY spray foam insulation kits cost $300 to $500 to cover 200 square feet with 1″ thickness, translating to approximately $0.50 to $2.00 per square foot for materials.
However, DIY applications come with limitations and challenges. Most retail kits are designed for small areas and touch-up work rather than whole-house applications. The equipment required for large-scale DIY projects can be expensive to rent or purchase, potentially negating the cost savings. Additionally, achieving proper foam density and coverage requires experience and technique that most homeowners lack.
Professional Installation Value Proposition
Professional installation typically costs 2-3 times more than DIY kits but provides significant advantages in terms of quality, warranty coverage, and safety. Professional contractors possess specialized equipment capable of maintaining proper chemical temperatures and mixing ratios for optimal foam performance. They also carry insurance coverage and provide warranties on their workmanship.
The complexity of spray foam chemistry and application techniques makes professional installation the preferred choice for most homeowners. Improper mixing, temperature control, or application can result in poor adhesion, inadequate R-values, and potential off-gassing issues that compromise both performance and indoor air quality.
Factors Affecting Spray Foam Insulation Pricing
Application Area Complexity
The complexity of the installation area significantly impacts labor costs and overall project pricing. Simple, accessible areas like open attics or basement walls typically command standard rates, while confined spaces, irregular geometries, or areas requiring extensive preparation work increase costs substantially.
Areas requiring electrical or plumbing modifications prior to foam application add both time and complexity to projects. Contractors may charge premium rates for installations requiring coordination with other trades or extensive masking and protection of adjacent surfaces.
Thickness Requirements
Insulation thickness directly correlates with material costs and application time. Thicker insulation means more material and higher costs, making it essential to understand your specific thickness requirements before obtaining quotes. Building codes in different climate zones specify minimum R-values that determine the required foam thickness.
Recommended Thickness Guidelines:
- Attic Applications: 6-10 inches depending on climate zone
- Wall Cavities: 2-4 inches for standard framing
- Basement Walls: 2-3 inches for interior applications
- Crawl Spaces: 3-4 inches for optimal moisture control
Preparation and Access Requirements
Site preparation requirements can significantly impact project costs. Areas requiring extensive cleaning, debris removal, or surface preparation will incur additional charges. Limited access areas may require specialized equipment or additional labor time, increasing overall project costs.
Safety considerations for working in confined spaces or at heights may require additional equipment and safety measures, contributing to higher labor costs. Some installations may require scaffolding, specialized ventilation, or extended curing times that affect project scheduling and pricing.
Long-Term Value and Return on Investment
While the initial spray foam insulation cost per square foot may seem high compared to traditional insulation materials, the long-term financial benefits often justify the investment. Spray foam insulation pays for itself in time because it improves energy efficiency by minimizing heat transfer throughout your home, resulting in substantial utility bill reductions.
Energy savings from spray foam insulation typically range from 15-50% depending on the home’s previous insulation condition and local climate. In areas with extreme temperatures, these savings can amount to hundreds or thousands of dollars annually, providing a reasonable return on investment within 5-10 years.
The durability of spray foam insulation adds to its long-term value proposition. Most polyurethane foam insulation lasts 80 to 100 years, far exceeding the lifespan of traditional insulation materials that may require replacement every 15-20 years. This longevity factor makes spray foam insulation a sound long-term investment for homeowners planning to remain in their homes.
Cost-Saving Strategies for Spray Foam Projects
Timing and Seasonal Considerations
Strategic timing can significantly impact spray foam insulation costs. Contractors often offer discounts during slower seasons, typically late fall through early spring when demand for insulation services decreases. However, extreme weather conditions may limit installation options during winter months in some regions.
Bundling spray foam installation with other home improvement projects can provide cost savings opportunities. Contractors may offer package deals when insulation work is combined with roofing, siding, or HVAC system upgrades, reducing overall project costs through shared mobilization and setup expenses.
Obtaining Multiple Quotes
Securing quotes from multiple contractors is essential for understanding local market rates and identifying competitive pricing. Request detailed quotes that break down material and labor costs separately, allowing for accurate comparisons between different contractors and foam types.
When evaluating quotes, consider factors beyond just price, including contractor experience, warranty offerings, and references from previous customers. The lowest bid may not always provide the best value if it compromises on quality or service.
Maximizing Energy Efficiency Incentives
Many utility companies and government agencies offer rebates and incentives for energy-efficient home improvements, including spray foam insulation. These programs can significantly offset initial installation costs, improving the overall return on investment for spray foam projects.
Federal tax credits for energy-efficient home improvements may apply to spray foam insulation installations that meet specific criteria. State and local programs may offer additional incentives, making it worthwhile to research available opportunities before proceeding with installation.
Common Spray Foam Installation Mistakes That Increase Costs
Understanding common installation mistakes can help homeowners avoid cost overruns and ensure project success. Inadequate surface preparation is a frequent issue that can compromise foam adhesion and require costly repairs or reapplication. Proper cleaning and moisture control are essential for optimal foam performance.
Temperature and humidity control during application significantly affect foam quality and coverage rates. Installations performed in unsuitable conditions may require additional material or remedial work, increasing project costs beyond initial estimates. Professional contractors understand these requirements and factor them into project planning and scheduling.
Incomplete coverage or inconsistent thickness can result in thermal bridging and reduced energy efficiency, negating the benefits of spray foam insulation. These issues may require additional foam application to achieve desired performance levels, adding unexpected costs to projects.
Maintenance and Longevity Considerations
Spray foam insulation requires minimal maintenance once properly installed, contributing to its long-term cost-effectiveness. However, periodic inspection is recommended to identify any damage from pests, moisture intrusion, or building settlement that could compromise performance.
The exceptional durability of spray foam insulation means homeowners can expect decades of reliable performance without replacement costs. This longevity factor should be considered when evaluating the true cost of spray foam insulation compared to alternatives that may require periodic replacement or maintenance.
Proper installation techniques and quality materials are essential for achieving maximum lifespan and performance from spray foam insulation. Choosing experienced contractors and premium foam formulations may increase initial costs but provide superior long-term value through enhanced durability and performance.
Ready to get accurate pricing for your spray foam insulation project? Contact qualified contractors in your area for detailed quotes on spray foam insulation cost and discover how much you can save on energy bills with professional installation. Get personalized estimates based on your specific square footage and project requirements.
Source: Spray Foam Insulation Cost Per Square Foot