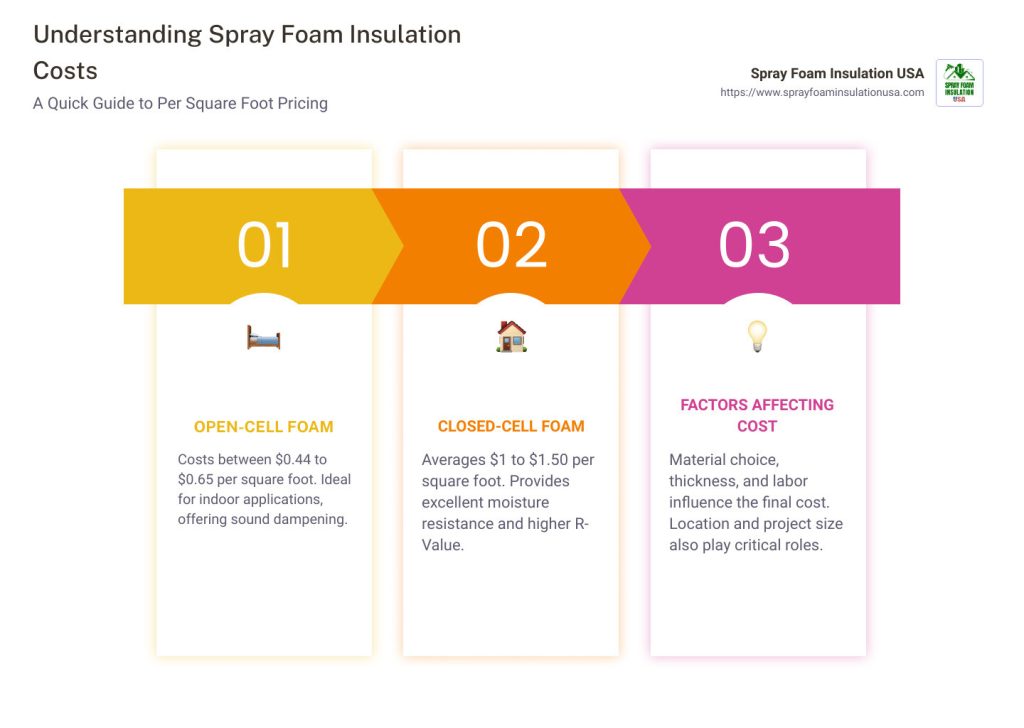
Understanding Spray Foam Cost in Today’s Market
When considering home insulation upgrades, spray foam cost remains one of the most critical factors homeowners evaluate. The investment in spray foam insulation can significantly impact your home’s energy efficiency, comfort, and long-term value. Understanding the various pricing components and factors that influence spray foam insulation costs helps you make informed decisions that align with your budget and energy-saving goals.
Spray foam insulation costs typically range from $1.00 to $4.50 per square foot, with most homeowners paying between $3,385 and $10,960 for complete home insulation projects. These prices reflect both material costs and professional installation services, making spray foam insulation a substantial but worthwhile investment for most properties.
The spray foam cost varies significantly based on several key factors including foam type, project size, location accessibility, and regional labor rates. Professional contractors typically charge between $50 and $100 per hour for installation services, with material costs accounting for approximately 40-60% of the total project expense.
Breaking Down Spray Foam Cost by Type
Open-Cell Spray Foam Pricing
Open-cell spray foam costs between $0.45 and $0.75 per board foot for materials, making it the more affordable option for homeowners working with tighter budgets. This type of foam expands significantly during application, creating excellent sound dampening properties while providing moderate insulation performance.
The lower spray foam cost for open-cell varieties makes them ideal for interior applications where moisture resistance isn’t a primary concern. Open-cell foam typically achieves R-values between 3.5 and 4.5 per inch, requiring thicker applications to match the performance of closed-cell alternatives.
Installation of open-cell spray foam generally proceeds faster than closed-cell applications, potentially reducing labor costs. However, the thickness requirements for achieving optimal R-values can offset some material cost savings, particularly in regions with extreme temperature variations.
Closed-Cell Spray Foam Investment
Closed-cell spray foam costs range from $1.00 to $1.60 per board foot, representing approximately double the material cost of open-cell options. This higher spray foam cost reflects the superior insulation performance, moisture resistance, and structural support properties that closed-cell foam provides.
The premium spray foam cost for closed-cell applications delivers exceptional R-values between 6.0 and 7.0 per inch, allowing for thinner applications while achieving superior insulation performance. This efficiency can reduce the overall square footage requirements, potentially balancing the higher per-foot material costs.
Closed-cell foam creates an effective vapor barrier, eliminating the need for additional moisture control measures in many applications. This integrated approach can reduce overall project costs by eliminating separate vapor barrier installation and associated labor expenses.
Factors Influencing Your Spray Foam Cost
Project Size and Scope
For an average 1,000 square foot project, spray foam companies typically charge labor costs between $1,500 and $5,000, depending on project scope, accessibility, complexity, and additional services. Larger projects generally benefit from economies of scale, reducing the per-square-foot spray foam cost through bulk material pricing and efficient labor utilization.
Small-scale projects often carry higher per-square-foot costs due to minimum service charges, equipment setup requirements, and travel expenses. Contractors typically establish minimum project sizes to ensure profitability, which can increase spray foam cost for homeowners with limited insulation needs.
Commercial and industrial projects involving thousands of square feet typically achieve the most favorable spray foam cost per square foot due to streamlined logistics, bulk material purchasing, and efficient crew deployment strategies.
Installation Complexity and Accessibility
The accessibility of the installation area significantly impacts the cost of attic and other spray foam applications. Areas requiring special equipment, confined space entry, or extensive preparation work command premium pricing due to increased labor requirements and safety considerations.
Crawl spaces, tight attic areas, and basement rim joists present unique challenges that can increase spray foam cost through specialized equipment requirements and slower application processes. These challenging locations often require additional safety measures, ventilation systems, and protective equipment that add to overall project expenses.
Multi-story applications, cathedral ceilings, and complex architectural features require scaffolding, lifts, or specialized access equipment that increases both labor time and equipment rental costs. These factors can increase spray foam cost by 20-40% compared to easily accessible ground-level applications.
Geographic Location and Regional Variations
The cost varies, influenced by factors like attic size, foam type (open-cell or closed-cell), labor costs, and geographic location. Urban areas typically command higher spray foam costs due to increased labor rates, transportation expenses, and higher operating costs for contractors.
Climate considerations also influence spray foam cost, as regions with extreme temperatures may require thicker applications or specialized foam formulations. Northern climates often necessitate higher R-value requirements, increasing material usage and associated costs.
Regional building codes and permit requirements can add to overall spray foam cost through mandatory inspections, specialized installation techniques, or additional documentation requirements. These regulatory factors vary significantly between jurisdictions and can impact project timelines and expenses.
Professional Installation vs. DIY Spray Foam Cost
Professional Installation Investment
Professional spray foam installation ensures optimal performance, warranty coverage, and compliance with building codes, justifying the higher spray foam cost through superior results and long-term reliability. On average, expect to pay between $1.50 and $3 per square foot for professional installation.
Professional contractors bring specialized equipment, technical expertise, and safety protocols that ensure proper foam application, curing, and performance. This expertise minimizes the risk of installation errors that could compromise insulation effectiveness or create safety hazards.
The professional installation spray foam cost includes equipment rental, safety gear, proper ventilation systems, and cleanup services that would otherwise represent additional expenses for DIY projects. Many contractors also provide warranties covering both materials and workmanship, adding value to the higher initial investment.
DIY Spray Foam Cost Considerations
To insulate an area of 1,000 sq ft, homeowners can expect to spend approximately $500 to $2,000 on DIY spray foam insulation. This significant cost reduction makes DIY applications attractive for budget-conscious homeowners with appropriate skills and safety equipment.
DIY spray foam kits typically include pre-measured components, application guns, and basic safety equipment, but may require additional purchases for adequate ventilation, protective gear, and cleanup supplies. These additional costs can increase the total DIY spray foam cost beyond initial kit pricing.
The learning curve associated with proper spray foam application can result in material waste, uneven coverage, or inadequate thickness, potentially increasing overall DIY spray foam cost through additional material purchases or professional correction services.
Cost-Benefit Analysis of Spray Foam Investment
Energy Savings and Payback Period
The higher initial spray foam cost compared to traditional insulation options generates substantial energy savings that offset the investment over time. Properly installed spray foam insulation can reduce heating and cooling costs by 30-50% annually, creating significant long-term value.
Most homeowners achieve payback on their spray foam cost investment within 5-10 years through reduced energy bills, improved comfort, and increased property value. The superior air sealing properties of spray foam eliminate drafts and thermal bridging that compromise the effectiveness of traditional insulation materials.
The longevity of spray foam insulation, typically lasting 30+ years without degradation, provides decades of energy savings that far exceed the initial spray foam cost. This durability eliminates the need for insulation replacement or maintenance that affects other insulation types.
Property Value Enhancement
Quality spray foam insulation adds measurable value to residential properties through improved energy efficiency ratings, enhanced comfort, and reduced maintenance requirements. Real estate professionals recognize spray foam insulation as a premium feature that appeals to energy-conscious buyers.
The spray foam cost investment typically returns 70-90% of the initial expense through increased property value, making it one of the most cost-effective home improvement projects. Energy-efficient homes command premium pricing in competitive real estate markets.
Modern home buyers increasingly prioritize energy efficiency, making the spray foam cost investment a strategic decision that enhances marketability and reduces time on market when selling.
Regional Spray Foam Cost Variations
Urban vs. Rural Pricing Differences
Metropolitan areas typically experience higher spray foam costs due to increased labor rates, transportation expenses, and higher business operating costs. Urban contractors may charge 20-40% more than rural counterparts, reflecting the higher cost of doing business in dense population centers.
Rural areas often benefit from lower spray foam costs due to reduced competition, lower overhead expenses, and streamlined logistics. However, rural homeowners may face limited contractor availability and longer project scheduling timelines.
The availability of materials and supplier networks affects spray foam cost in different regions, with remote areas potentially experiencing higher material costs due to transportation expenses and limited distribution networks.
Climate-Driven Cost Factors
Northern climates requiring higher R-value insulation naturally experience higher spray foam costs due to increased material requirements and thicker applications. These regions may require 4-6 inches of closed-cell foam compared to 2-3 inches in moderate climates.
Humid coastal regions may necessitate closed-cell foam applications for moisture control, increasing spray foam cost compared to inland areas where open-cell foam provides adequate performance. The moisture resistance properties of closed-cell foam justify the higher investment in these challenging environments.
Extreme temperature variations require careful consideration of foam expansion and contraction properties, potentially requiring specialized formulations that increase material costs and overall spray foam cost.
Spray Foam Cost Comparison with Alternative Insulation
Traditional Insulation Cost Analysis
Fiberglass batt insulation typically costs $0.50-$1.50 per square foot installed, representing significant savings compared to spray foam cost. However, fiberglass insulation provides inferior air sealing properties and may require additional vapor barriers and air sealing measures.
Blown-in cellulose insulation costs $1.00-$2.50 per square foot, offering better air sealing than fiberglass but still requiring separate air sealing measures. The total cost of achieving equivalent performance to spray foam often narrows the initial cost gap significantly.
Rigid foam board insulation costs $1.50-$3.50 per square foot installed, approaching spray foam cost levels while providing inferior air sealing properties. The labor-intensive installation process and sealing requirements can make rigid foam installations as expensive as spray foam applications.
Performance-Based Cost Evaluation
When evaluating spray foam cost against alternatives, consider the total cost of achieving equivalent insulation performance, air sealing, and moisture control. Spray foam provides multiple functions in a single application, often eliminating the need for separate air barriers, vapor barriers, and additional insulation layers.
The superior R-value per inch of spray foam insulation allows for thinner applications in space-constrained areas, potentially eliminating the need for structural modifications or reduced interior space. This space efficiency can offset higher spray foam costs through avoided construction expenses.
The longevity and maintenance-free nature of spray foam insulation eliminates replacement costs and maintenance expenses associated with traditional insulation materials. This long-term cost advantage makes spray foam cost competitive over the building’s lifecycle.
Smart Strategies for Managing Spray Foam Cost
Project Planning and Timing
Scheduling spray foam installation during contractors’ slower seasons can reduce labor costs and improve project scheduling flexibility. Many contractors offer discounts during winter months or early spring when demand typically decreases.
Combining multiple insulation projects or coordinating with other home improvement activities can reduce overall spray foam cost through shared mobilization expenses, bulk material pricing, and efficient crew utilization.
Planning ahead allows for competitive bidding, material price comparison, and contractor selection based on value rather than availability. Rush projects typically command premium pricing that increases spray foam cost unnecessarily.
Contractor Selection and Negotiation
Obtaining multiple quotes from qualified contractors ensures competitive spray foam cost pricing and helps identify potential cost-saving opportunities. Reputable contractors should provide detailed breakdowns of material and labor costs for comparison purposes.
Evaluating contractor qualifications, insurance coverage, and warranty terms helps ensure that spray foam cost investments deliver long-term value through quality installation and reliable service support.
Negotiating project scope, material specifications, and payment terms can reduce spray foam cost while maintaining quality standards. Many contractors offer flexible payment options or seasonal discounts that improve project affordability.
Maximizing Value from Your Spray Foam Investment
Quality Assurance and Inspection
Proper installation techniques and quality control measures ensure that spray foam cost investments deliver expected performance and longevity. Reputable contractors provide installation documentation and performance guarantees that protect homeowner investments.
Third-party inspections and thermal imaging verification can identify installation defects or coverage gaps that compromise spray foam performance. These quality assurance measures justify higher spray foam costs through improved reliability and performance.
Regular maintenance and monitoring of spray foam installations ensures optimal performance throughout the insulation’s service life. Proper maintenance protects the spray foam cost investment and maintains energy efficiency benefits.
Integration with Other Energy Efficiency Measures
Combining spray foam insulation with other energy efficiency improvements creates synergistic benefits that maximize return on investment. HVAC system upgrades, window replacements, and weatherization measures complement spray foam installations for optimal energy performance.
The superior air sealing properties of spray foam insulation may allow for smaller, more efficient HVAC systems, reducing equipment costs and operating expenses. This system downsizing can offset higher spray foam costs through reduced equipment investment.
Utility rebates and tax incentives for energy efficiency improvements can reduce net spray foam cost while enhancing overall project economics. Many utility companies offer substantial rebates for spray foam installations that meet energy efficiency standards.
Spray Foam Cost Considerations for Different Applications
Attic Insulation Investment
Attic spray foam insulation costs vary based on factors like attic size, foam type (open-cell or closed-cell), labor costs, and geographic location. Attic applications typically benefit from easier access and straightforward installation, potentially reducing labor costs compared to other applications.
The choice between open-cell and closed-cell foam for attic applications significantly impacts spray foam cost, with closed-cell foam providing superior moisture resistance and structural support at higher material costs. Climate considerations often drive this decision, with humid regions favoring closed-cell applications.
Attic spray foam installations eliminate the need for separate vapor barriers and air sealing measures, reducing overall project costs while providing superior performance compared to traditional insulation methods.
Basement and Crawl Space Costs
Basement and crawl space spray foam applications often require closed-cell foam for moisture control, increasing spray foam cost compared to attic applications. These challenging environments demand superior moisture resistance and structural support properties.
Limited access and confined working conditions in basements and crawl spaces can increase labor costs and project timelines. Special equipment requirements and safety considerations add to overall spray foam cost in these applications.
The moisture control benefits of spray foam insulation in basements and crawl spaces eliminate the need for separate waterproofing measures, potentially offsetting higher spray foam costs through avoided construction expenses.
Wall Insulation Pricing
Existing wall insulation projects require specialized injection techniques or wall opening procedures that increase spray foam cost compared to new construction applications. These retrofit applications demand skilled technicians and specialized equipment.
The choice between interior and exterior wall insulation affects spray foam cost through different access requirements and installation complexities. Exterior applications may require siding removal and weatherproofing considerations that increase project expenses.
Wall spray foam installations in new construction benefit from easy access and straightforward application techniques, typically achieving the most favorable spray foam cost per square foot for residential applications.
Understanding Quality vs. Price in Spray Foam Cost
Material Quality Considerations
Premium spray foam materials command higher prices but deliver superior performance, longevity, and environmental safety. The spray foam cost differential between budget and premium materials often justifies itself through improved performance and reduced long-term maintenance requirements.
Environmentally friendly spray foam formulations may carry higher material costs but provide better indoor air quality and reduced environmental impact. These premium materials often justify higher spray foam costs through health and environmental benefits.
The chemical composition and manufacturing quality of spray foam materials significantly impact performance characteristics, curing time, and installation requirements. Higher quality materials typically require less material waste and provide more consistent application results.
Installation Quality Factors
Skilled installation techniques and proper equipment ensure optimal spray foam performance regardless of material quality. The spray foam cost investment in experienced contractors typically delivers superior results and long-term reliability.
Proper surface preparation, environmental controls, and application techniques significantly impact spray foam performance and longevity. These quality factors justify higher spray foam costs through improved installation results and reduced callback requirements.
Quality control measures and performance verification ensure that spray foam cost investments deliver expected energy savings and comfort improvements. Reputable contractors provide documentation and warranties that protect homeowner investments.
Future-Proofing Your Spray Foam Investment
Technology Advances and Cost Trends
Emerging spray foam technologies and improved formulations continue to enhance performance while potentially reducing spray foam cost through manufacturing efficiencies and improved application techniques. Staying informed about technology advances helps optimize investment timing.
Market competition and manufacturing scale improvements gradually reduce spray foam costs while maintaining or improving performance characteristics. Long-term cost trends favor increased adoption and improved affordability of spray foam insulation.
Building code evolution and energy efficiency standards increasingly favor spray foam insulation, potentially affecting future spray foam cost through increased demand and regulatory requirements.
Maintenance and Lifecycle Considerations
Proper maintenance and monitoring of spray foam installations ensure optimal performance throughout the insulation’s service life. These maintenance practices protect spray foam cost investments and maintain energy efficiency benefits.
The exceptional longevity of spray foam insulation, typically 30+ years without degradation, provides decades of energy savings that justify initial spray foam cost investments. This durability eliminates replacement costs associated with traditional insulation materials.
Future building modifications and renovations should consider existing spray foam installations to protect initial investments and maintain energy efficiency performance. Proper planning preserves spray foam cost investments during future construction activities.
Frequently Asked Questions About Spray Foam Cost
What factors most significantly affect spray foam cost?
The primary factors influencing spray foam cost include foam type (open-cell vs. closed-cell), project size, installation complexity, geographic location, and contractor expertise. Several factors influence the cost of spray foam insulation, including the type of material, labor expenses, project complexity, and geographical location.
How does spray foam cost compare to traditional insulation?
While spray foam cost initially appears higher than traditional insulation, the superior air sealing properties, higher R-values per inch, and elimination of additional air barriers often make total system costs competitive. The energy savings and longevity of spray foam typically justify the higher initial investment.
Can I reduce spray foam cost through DIY installation?
DIY spray foam installation can significantly reduce costs, with homeowners expecting to spend approximately $500 to $2,000 on DIY spray foam insulation for 1,000 square feet. However, proper installation requires specialized equipment, safety protocols, and technical expertise that may justify professional installation costs.
What is the average payback period for spray foam cost investments?
Most homeowners achieve payback on spray foam cost investments within 5-10 years through reduced energy bills and improved comfort. The superior air sealing properties of spray foam can reduce heating and cooling costs by 30-50% annually, creating substantial long-term value.
Does spray foam cost vary significantly by region?
Yes, spray foam cost varies substantially by geographic region due to differences in labor rates, material availability, climate requirements, and local building codes. Urban areas typically experience higher costs than rural regions, while northern climates may require thicker applications that increase material costs.
How thick should spray foam be for optimal performance?
Thickness may have the biggest impact on spray foam insulation cost. One-inch open-cell foam can cost as little as $0.44 per square foot, while 3-inch closed-cell foam can run as high as $8.70 per square foot. The optimal thickness depends on climate zone, application area, and desired R-value requirements.
Are there financing options available for spray foam cost?
Many contractors offer financing options for spray foam installations, including payment plans, low-interest loans, and seasonal promotions. Additionally, utility rebates and tax incentives can reduce net spray foam cost while improving project economics.
How do I verify that spray foam cost quotes are competitive?
Obtain multiple detailed quotes from qualified contractors, compare material specifications and labor rates, and verify contractor credentials and insurance coverage. Ensure quotes include all necessary services such as preparation, cleanup, and warranty coverage for accurate cost comparisons.
Looking for competitive spray foam cost estimates? Contact qualified insulation contractors in your area for detailed quotes and professional recommendations.
For comprehensive home security solutions, consider exploring best pepper spray for self defense options to complement your home safety measures.
Sources: