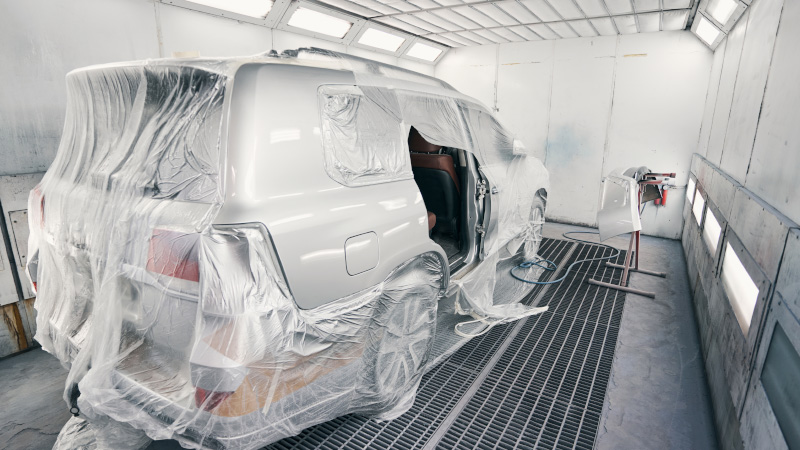
Whether you’re running an automotive shop, manufacturing facility, or custom fabrication business, a spray booth is essential for achieving professional-quality finishes while maintaining safety standards. These specialized enclosures provide controlled environments for applying paints, coatings, and other finishing materials, ensuring consistent results while protecting workers and the surrounding environment from harmful overspray and fumes.
In this comprehensive guide, we’ll explore everything you need to know about spray booths, from basic concepts to advanced selection criteria. By the end of this article, you’ll have the knowledge to make informed decisions about spray booth investments for your business.
What is a Spray Booth and Why Do You Need One?
A spray booth is a specialized enclosure designed to contain and control the application of liquid coatings, paints, and other finishing materials. These systems combine ventilation, filtration, and safety features to create an optimal environment for spray finishing operations while protecting workers and the environment from hazardous materials.
Modern spray booths serve multiple critical functions beyond simple containment. They provide consistent airflow patterns that help achieve uniform coating application, remove hazardous vapors and particles from the work environment, and prevent contamination from dust and debris that could compromise finish quality. Additionally, they help businesses comply with environmental regulations and workplace safety standards that govern the use of volatile organic compounds (VOCs) and hazardous air pollutants.
The investment in a quality spray booth system pays dividends through improved finish quality, reduced material waste, enhanced worker safety, and regulatory compliance. Without proper containment and ventilation, spray finishing operations can result in poor surface quality, health hazards, environmental violations, and significant cleanup costs.
Types of Spray Booths: Understanding Your Options
Cross-Draft Spray Booths
Cross-draft spray booths represent the most economical entry point into professional spray finishing systems. In these configurations, air enters through filtered openings on one side of the booth and exits through exhaust filters on the opposite side, creating a horizontal airflow pattern across the work area.
The primary advantage of cross-draft designs lies in their simplicity and lower initial cost compared to other configurations. They’re particularly well-suited for smaller operations, hobbyist applications, and businesses with limited budgets. Installation requirements are typically less complex, and maintenance costs tend to be lower due to the straightforward airflow design.
However, cross-draft booths do have limitations that users should consider. The horizontal airflow can cause overspray to drift across the work surface, potentially affecting finish quality on complex shapes or when multiple operators are working simultaneously. Additionally, the operator works within the airflow path, which may expose them to more overspray particles compared to downdraft configurations.
Downdraft Spray Booths
Downdraft spray booths represent the gold standard in professional finishing operations, utilizing a vertical airflow pattern that moves air from the ceiling down through the work area and exits through floor-level exhaust systems. This configuration creates the most controlled environment for spray applications, making it the preferred choice for high-end automotive refinishing, aerospace applications, and precision manufacturing.
The vertical airflow pattern in downdraft systems provides several significant advantages over other configurations. Overspray particles are immediately drawn away from the work surface and operator, reducing contamination and improving finish quality. The consistent airflow eliminates dead spots and turbulence that can cause uneven coating application or surface defects. Workers operate in the cleanest air zone, as fresh filtered air continuously flows down from above.
While downdraft spray booth installations require higher initial investments and more complex infrastructure, including raised floors or pit systems for exhaust air handling, the superior results often justify the additional costs. Many businesses find that the improved finish quality, reduced rework rates, and enhanced efficiency more than offset the higher upfront expenses.
Side-Draft Spray Booths
Side-draft spray booths offer a middle ground between cross-draft and downdraft configurations, utilizing vertical wall sections for air intake and exhaust. Air typically enters through filtered openings in the upper portions of the side walls and exits through lower exhaust points, creating a diagonal airflow pattern through the work area.
This configuration provides better overspray control than cross-draft systems while requiring less complex infrastructure than downdraft installations. Side-draft booths work well for operations that need improved performance over basic cross-draft designs but cannot justify the investment in downdraft systems. They’re particularly effective for medium-sized operations handling a variety of work pieces.
The diagonal airflow pattern in side-draft systems helps direct overspray away from critical work areas while maintaining reasonable air velocities for effective contamination control. Installation costs typically fall between cross-draft and downdraft options, making them attractive for businesses seeking performance improvements without maximum investment levels.
Key Components of Professional Spray Booth Systems
Ventilation and Airflow Management
The heart of any effective spray booth lies in its ventilation system, which must provide adequate air movement to capture and remove overspray particles and hazardous vapors while maintaining proper air velocities for optimal coating application. Professional systems typically maintain air velocities between 75-125 feet per minute at the work surface, though specific requirements vary based on coating types and application methods.
Airflow uniformity throughout the work area is crucial for consistent results. Well-designed systems minimize turbulence and dead spots that can cause uneven coating distribution or allow contamination to settle on work surfaces. This requires careful attention to inlet and exhaust sizing, positioning, and the internal geometry of the booth structure.
Modern spray booth ventilation systems incorporate variable speed drives and automated controls that allow operators to adjust air velocities based on specific application requirements. This flexibility helps optimize energy consumption while maintaining proper safety margins and finish quality standards.
Filtration Systems
Spray booth filters serve dual purposes: protecting downstream equipment and the environment while maintaining air quality within the work area. Intake filters remove dust, pollen, and other contaminants from outside air before it enters the booth, while exhaust filters capture overspray particles before air is released to the atmosphere.
Intake filtration typically employs multi-stage systems starting with coarse pre-filters that remove larger particles and extending to fine filters that eliminate smaller contaminants. High-efficiency particulate air (HEPA) filters may be used in critical applications requiring the cleanest possible air supply. Proper filtration prevents contamination that can cause surface defects like fisheyes, craters, and embedded particles.
Exhaust filtration systems must be designed to handle the specific characteristics of the materials being sprayed. Paint overspray filters utilize progressively denser media to capture particles of varying sizes, while specialized filters may be required for unusual coating chemistries or high-temperature applications. Regular filter maintenance and replacement schedules are essential for maintaining system performance and regulatory compliance.
Lighting Systems
Proper illumination in spray booth environments is critical for achieving consistent, high-quality finishes. Professional systems typically provide 50-100 foot-candles of evenly distributed light throughout the work area, with higher levels often preferred for critical color-matching applications.
LED lighting systems have become the standard for modern spray booth installations due to their energy efficiency, long service life, and superior color rendering properties. Unlike traditional fluorescent or incandescent systems, LEDs generate minimal heat and can operate safely in solvent-laden atmospheres when properly rated for hazardous locations.
Lighting uniformity is as important as overall light levels. Shadows, hot spots, and color variations can make it impossible to evaluate coating appearance accurately, leading to poor quality control and customer dissatisfaction. Professional installations often incorporate multiple light sources and reflective surfaces to achieve optimal illumination patterns.
Safety Features and Regulatory Compliance
Fire Suppression Systems
Spray booth fire protection systems are mandatory in most jurisdictions and represent one of the most critical safety features in any installation. These systems must be designed specifically for the unique hazards present in coating operations, including flammable solvents, overspray accumulation, and potential ignition sources.
Automatic sprinkler systems designed for spray booth applications utilize deluge-type configurations that flood the entire booth area when activated. These systems often incorporate specialized nozzles and water additives that improve fire suppression effectiveness while minimizing damage to equipment and work pieces. Pre-action systems that require two independent activation signals are sometimes used to prevent accidental discharge.
Dry chemical suppression systems may be preferred in applications where water damage would be particularly costly or where specialized fire risks exist. These systems can provide rapid fire knockdown while minimizing collateral damage, though they typically require more extensive cleanup after activation.
Explosion Prevention
The combination of flammable vapors and potential ignition sources in spray booth operations creates significant explosion risks that must be carefully managed through proper design and operating procedures. Electrical equipment must be rated for hazardous locations and installed according to strict codes that minimize spark potential.
Static electricity generation and accumulation present particular challenges in spray finishing operations. Grounding systems for all conductive objects, anti-static flooring materials, and humidity control help minimize static buildup that could provide ignition sources. Operators must use proper grounding techniques and personal protective equipment designed to prevent static discharge.
Vapor concentration monitoring systems can provide early warning of potentially dangerous conditions before explosive mixtures develop. These systems continuously sample air within the booth and trigger alarms or automatic shutdown sequences when vapor levels approach hazardous thresholds.
Environmental Controls
Modern spray booth installations must comply with increasingly stringent environmental regulations governing volatile organic compound (VOC) emissions and hazardous air pollutants. Compliance requires careful attention to capture efficiency, emission control technologies, and record-keeping requirements.
Thermal oxidizers, catalytic oxidizers, and other emission control devices may be required to achieve permitted emission levels. These systems destroy VOCs and other pollutants before they are released to the atmosphere, though they add significant complexity and operating costs to spray booth operations.
Monitoring and record-keeping systems help demonstrate ongoing compliance with environmental permits and regulations. Automated data collection systems can simplify compliance reporting while providing operational feedback that helps optimize system performance.
Spray Booth Selection Criteria: Making the Right Choice
Assessing Your Application Requirements
Selecting the optimal spray booth configuration begins with a thorough analysis of your specific application requirements, including the types of coatings you’ll be applying, the size and variety of work pieces you’ll be finishing, and your desired production rates. These factors directly influence booth size, airflow requirements, and specialized features you’ll need.
Different coating materials have varying application characteristics that affect booth design requirements. Water-based coatings typically require different temperature and humidity conditions compared to solvent-based systems, while specialty coatings like primers, base coats, and clear coats may have unique curing requirements. High-solids coatings produce less overspray but may require higher air velocities for proper atomization, while low-solids materials create more overspray that must be effectively captured.
Work piece size and configuration significantly impact booth sizing decisions. Large items like trucks, buses, or industrial equipment require substantial booth dimensions and higher air volumes, while smaller parts may be efficiently processed in compact systems. Complex shapes with recessed areas or internal cavities may require specialized airflow patterns or additional air movement systems to ensure complete coverage and proper drying.
Size and Capacity Considerations
Spray booth sizing involves balancing immediate needs with future growth potential while considering space constraints and budget limitations. Undersized booths restrict operational flexibility and may compromise finish quality, while oversized systems waste energy and increase operating costs unnecessarily.
Booth length should accommodate your longest work pieces with adequate clearance for equipment movement and operator access. Width requirements depend on work piece dimensions and whether you need to accommodate multiple items simultaneously. Height considerations include work piece dimensions, overhead clearance for lifting equipment, and space for lighting and ventilation components.
Air volume requirements scale with booth size and must provide adequate air changes per hour for effective contamination control. Larger booths require proportionally higher air volumes, which increase energy consumption and equipment costs. Careful analysis of actual requirements helps optimize system sizing for efficiency and performance.
Booth Size Category | Typical Dimensions | Air Volume (CFM) | Common Applications |
---|---|---|---|
Small/Portable | 8′ x 8′ x 8′ | 2,000-4,000 | Small parts, hobby use |
Medium | 14′ x 8′ x 8′ | 6,000-10,000 | Automotive panels, furniture |
Large | 24′ x 14′ x 10′ | 15,000-25,000 | Complete vehicles, large equipment |
Industrial | 40′ x 20′ x 12′ | 30,000+ | Trucks, buses, industrial equipment |
Budget and ROI Analysis
Spray booth investments represent significant capital expenditures that require careful financial analysis to ensure appropriate returns. Initial costs include equipment purchase, installation, facility modifications, and startup expenses, while ongoing costs encompass energy consumption, filter replacement, maintenance, and regulatory compliance activities.
Quality improvements achievable with professional spray booth systems often justify higher initial investments through reduced rework rates, improved customer satisfaction, and enhanced reputation. Quantifying these benefits requires analysis of current rejection rates, rework costs, and potential revenue increases from improved capabilities.
Energy efficiency considerations have become increasingly important as utility costs rise and environmental awareness grows. Modern systems incorporate variable speed drives, heat recovery systems, and automated controls that can significantly reduce operating costs compared to older designs. Payback periods for efficiency upgrades often range from 2-5 years depending on usage levels and local utility rates.
Installation and Setup Best Practices
Site Preparation Requirements
Successful spray booth installation begins with thorough site preparation that addresses structural, electrical, and mechanical requirements. Foundation requirements vary significantly based on booth type and size, with downdraft systems requiring substantial excavation for pit construction or raised floor installation.
Electrical infrastructure must accommodate significant power requirements for ventilation equipment, lighting systems, and auxiliary equipment. Professional installations typically require 480V three-phase power for larger systems, along with specialized hazardous location wiring methods throughout the spray area. Coordination with local electrical codes and permit requirements is essential.
Mechanical infrastructure includes compressed air systems for spray equipment, water supplies for fire protection systems, and natural gas or propane connections for heating systems. Proper sizing and installation of these utilities prevent operational limitations and ensure code compliance.
Professional Installation vs. DIY
While smaller spray booth systems may seem suitable for self-installation, professional installation typically provides better results and fewer long-term problems. Experienced installers understand code requirements, permit processes, and installation best practices that prevent costly mistakes and ensure optimal performance.
Professional installers typically offer warranties on their work and can provide ongoing service support that helps maintain system performance over time. They also have relationships with code officials and inspectors that can smooth the approval process and prevent delays.
DIY installation may be appropriate for simpler systems in non-critical applications, but requires significant research and planning to avoid problems. Local code requirements, permit processes, and inspection procedures must be thoroughly understood before beginning any installation project.
Commissioning and Testing
Proper spray booth commissioning ensures that installed systems meet design specifications and operate safely before beginning production use. This process typically includes airflow verification, filter testing, control system calibration, and safety system testing.
Airflow testing verifies that air velocities and patterns meet design requirements throughout the work area. This testing often reveals installation issues that must be corrected before the system can operate properly. Professional commissioning includes detailed documentation of test results for future reference and regulatory compliance.
Control system testing ensures that all automated functions operate correctly and safety interlocks function as designed. This includes testing emergency shutdown systems, alarm functions, and any automated material handling equipment integrated with the booth system.
Maintenance and Operations Guide
Daily Operating Procedures
Effective spray booth maintenance begins with consistent daily operating procedures that help identify potential problems before they affect system performance or safety. Pre-shift inspections should include visual checks of filters, airflow indicators, lighting systems, and safety equipment.
Filter condition monitoring is crucial for maintaining proper airflow and system performance. Pressure differential gauges provide objective measurements of filter loading that indicate when replacement is necessary. Visual inspection can identify obvious problems like tears, bypassing, or unusual loading patterns that require immediate attention.
Safety system checks ensure that fire suppression systems, emergency shutdown controls, and personal protective equipment remain functional. Daily verification of these systems helps prevent accidents and ensures regulatory compliance.
Preventive Maintenance Schedules
Systematic spray booth maintenance programs extend equipment life, maintain performance levels, and prevent costly breakdowns that disrupt production schedules. Maintenance schedules should be based on manufacturer recommendations, operating conditions, and historical performance data.
Filter replacement represents the most frequent maintenance requirement, with schedules varying based on usage levels and contamination sources. Intake filters typically require monthly replacement in normal conditions, while exhaust filters may last 3-6 months depending on coating types and spray volumes.
Mechanical equipment maintenance includes fan belt inspection and replacement, motor lubrication, and bearing inspection. Electrical system maintenance covers control panel inspection, connection tightness checks, and lighting system maintenance. Documentation of all maintenance activities helps track costs and identify trends that may indicate impending problems.
Troubleshooting Common Issues
Spray booth problems often manifest as finish quality issues, unusual operating costs, or safety concerns that require systematic diagnosis and correction. Airflow problems are among the most common issues, typically caused by filter restrictions, fan problems, or ductwork obstructions.
Poor finish quality can result from contamination, improper airflow patterns, or equipment malfunctions. Systematic evaluation helps identify root causes and appropriate corrective actions. Common causes include inadequate filtration, cross-contamination between colors, or improper temperature and humidity conditions.
Energy consumption increases often indicate filter loading, equipment wear, or control system problems. Trending utility costs and comparing them to production levels helps identify efficiency problems before they become severe.
Cost Analysis and Return on Investment
Initial Investment Breakdown
Spray booth costs vary dramatically based on size, configuration, and feature requirements, making detailed cost analysis essential for budgeting and financial planning. Basic cross-draft systems suitable for small operations may cost $15,000-$30,000, while large downdraft installations can exceed $200,000 including installation and auxiliary equipment.
Equipment costs typically represent 60-70% of total project costs, with installation, permits, and facility modifications comprising the remainder. Hidden costs often include electrical upgrades, compressed air systems, and structural modifications that may not be obvious during initial planning phases.
Financing options include traditional equipment loans, leasing arrangements, and specialized financing programs offered by some manufacturers. Lease options may be attractive for businesses with limited capital or uncertain long-term requirements, though total costs are typically higher than purchase options.
Operating Cost Considerations
Ongoing spray booth operating costs include energy consumption, filter replacement, maintenance, and regulatory compliance activities. Energy typically represents the largest operating expense, with costs varying based on local utility rates, usage patterns, and equipment efficiency levels.
Filter replacement costs depend on usage levels, coating types, and filter quality. Higher-quality filters often provide longer service life and better performance, justifying their higher initial costs through reduced replacement frequency and improved system performance.
Maintenance costs include both routine preventive maintenance and emergency repairs. Well-maintained systems typically experience fewer breakdowns and longer equipment life, making preventive maintenance programs cost-effective investments.
Payback Period Calculations
Spray booth ROI analysis requires careful evaluation of both cost savings and revenue enhancements achievable through improved finishing capabilities. Cost savings may include reduced material waste, lower rework rates, and improved energy efficiency compared to existing systems.
Revenue enhancements often result from improved finish quality, faster production rates, and expanded service capabilities that command premium pricing. Quantifying these benefits requires analysis of current performance levels and realistic projections of improvements achievable with new equipment.
Typical payback periods range from 2-7 years depending on usage levels, cost savings achieved, and revenue enhancements realized. High-volume operations typically achieve faster paybacks due to greater utilization of system capabilities and cost savings potential.
Future Trends and Technology Advances
Smart Booth Technologies
Modern spray booth technology increasingly incorporates smart sensors, automated controls, and data analytics that optimize performance while reducing operating costs. Internet of Things (IoT) sensors monitor critical parameters like airflow, temperature, humidity, and filter condition, providing real-time feedback that helps optimize operations.
Automated control systems adjust operating parameters based on coating requirements, environmental conditions, and production schedules. These systems can optimize energy consumption, maintain consistent environmental conditions, and provide predictive maintenance alerts that prevent unexpected breakdowns.
Data analytics platforms collect and analyze operating data to identify optimization opportunities, predict maintenance requirements, and benchmark performance against industry standards. This information helps operators make informed decisions about system improvements and operational changes.
Environmental Sustainability
Increasing environmental awareness and regulatory requirements are driving development of more sustainable spray booth solutions. Heat recovery systems capture waste heat from exhaust air and use it to warm incoming air, reducing energy consumption and operating costs.
Solvent recovery systems capture and recycle solvents from exhaust air, reducing raw material costs while minimizing environmental emissions. These systems are particularly attractive for operations using expensive solvents or facing strict emission limits.
Water-based coating systems are gaining popularity due to their reduced environmental impact and improved worker safety characteristics. However, these systems often require different booth configurations and environmental controls compared to traditional solvent-based systems.
Automation Integration
Automated spray booth systems are becoming more common as labor costs increase and consistency requirements become more stringent. Robotic spray systems provide consistent application patterns, reduce operator exposure to hazardous materials, and can operate continuously without breaks or shift changes.
Automated material handling systems move work pieces through the finishing process without manual intervention, improving efficiency while reducing contamination risks. These systems often integrate with manufacturing execution systems that optimize production schedules and track work piece progress.
Quality control systems using machine vision and spectroscopy can automatically inspect finished surfaces and identify defects that require correction. These systems provide objective quality measurements and can trigger automatic rework procedures when problems are detected.
Conclusion: Making the Right Spray Booth Investment
Selecting and implementing the right spray booth system for your operation requires careful analysis of your specific requirements, available budget, and long-term business objectives. The investment in professional finishing equipment pays dividends through improved quality, enhanced safety, regulatory compliance, and operational efficiency that can provide competitive advantages in demanding markets.
Success with spray booth systems depends on proper selection, professional installation, comprehensive training, and ongoing maintenance programs that preserve performance and extend equipment life. While initial costs may seem substantial, the long-term benefits of improved finishing capabilities typically justify the investment through reduced costs, improved quality, and enhanced business opportunities.
As technology continues to advance and environmental regulations become more stringent, spray booth systems will continue evolving to provide better performance, lower operating costs, and reduced environmental impact. Staying informed about these developments helps ensure that your finishing operations remain competitive and compliant in an ever-changing business environment.
Whether you’re upgrading existing equipment or installing your first professional spray booth, the key to success lies in thorough planning, realistic expectations, and commitment to proper operation and maintenance practices that maximize your investment returns.