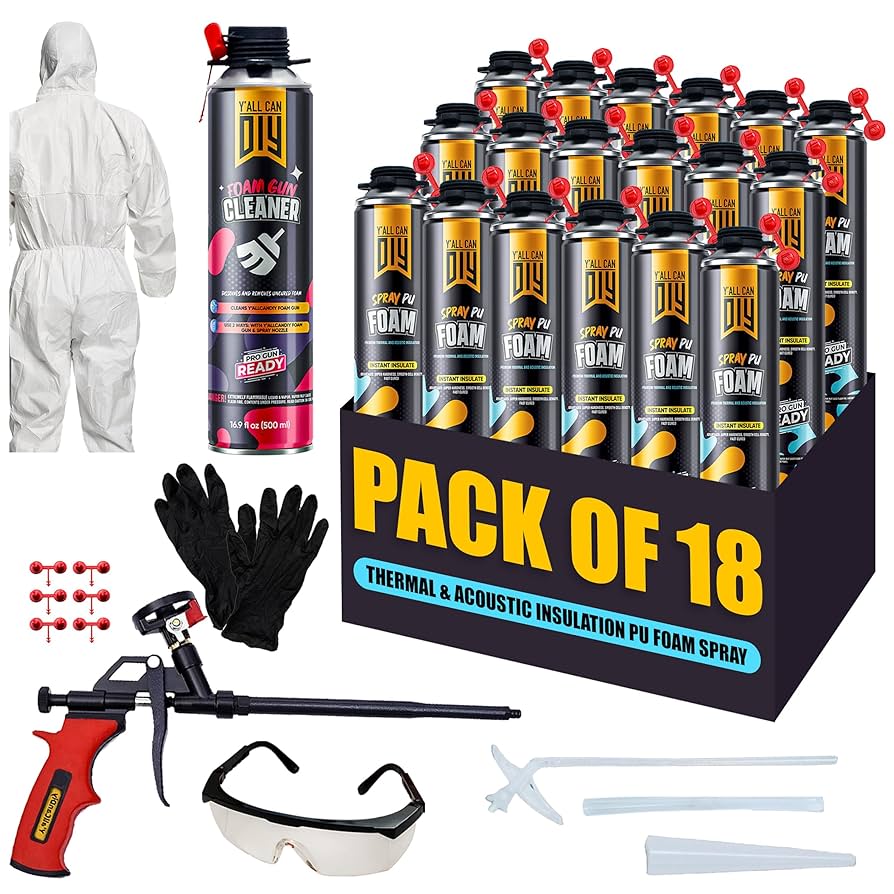
Are you tired of skyrocketing energy bills and drafty rooms that never seem to maintain a comfortable temperature? Closed cell spray foam kits offer homeowners and contractors a powerful solution to achieve superior insulation performance while maintaining complete control over their project timeline and budget. Unlike traditional insulation materials that can leave gaps and thermal bridges, closed cell spray foam creates a seamless barrier that delivers exceptional thermal resistance, moisture control, and structural reinforcement all in one application.
The growing popularity of closed cell spray foam kits stems from their ability to provide professional-grade insulation results without the need for expensive contractor services. These comprehensive kits contain everything needed to apply high-performance spray foam insulation, including specialized chemicals, application equipment, and safety gear. With proper preparation and technique, DIY enthusiasts can achieve R-values of 6-7 per inch of thickness, significantly outperforming traditional fiberglass batts or blown-in cellulose insulation.
What Are Closed Cell Spray Foam Kits?
Closed cell spray foam kits represent a revolutionary approach to DIY insulation that brings professional-grade performance directly to homeowners and small contractors. These comprehensive packages contain two-component polyurethane foam systems that chemically react when mixed, expanding to create a rigid, closed-cell foam structure with exceptional insulating properties. The “closed cell” designation refers to the foam’s cellular structure, where individual cells are completely enclosed, preventing air and moisture infiltration while providing superior thermal resistance.
The fundamental chemistry behind closed cell spray foam kits involves the reaction between isocyanate (A-side) and polyol resin (B-side) components. When these chemicals combine through the kit’s mixing equipment, they undergo an exothermic reaction that creates carbon dioxide gas, causing the mixture to expand dramatically. This expansion allows the foam to fill every crack, crevice, and irregular surface, creating a seamless insulation barrier that traditional materials simply cannot match.
Modern closed cell spray foam kits typically include pre-pressurized tanks or containers, specialized spray guns or applicators, mixing chambers, hoses, and comprehensive safety equipment. The foam produced has a density ranging from 1.7 to 2.0 pounds per cubic foot, significantly denser than open-cell foam alternatives. This density translates to superior structural properties, with closed cell foam adding measurable strength to walls, roofs, and other building components.
Key Components of Professional-Grade Kits
Component | Function | Typical Specifications |
---|---|---|
A-Side Chemical | Isocyanate component | 50% of total volume |
B-Side Chemical | Polyol resin blend | 50% of total volume |
Spray Gun | Chemical mixing/application | 1,000+ PSI operating pressure |
Hoses | Chemical transport | 15-25 feet length |
Safety Equipment | Personal protection | Respirator, gloves, coveralls |
The sophisticated formulation of closed cell spray foam kits ensures optimal performance across a wide range of environmental conditions. Advanced formulations include catalysts that control reaction speed, blowing agents that optimize cell structure, and additives that enhance fire resistance and long-term stability. These carefully engineered systems deliver consistent results when applied according to manufacturer specifications, making professional-quality insulation accessible to DIY applications.
Benefits of Using Closed Cell Spray Foam Kits
Closed cell spray foam kits deliver a comprehensive range of benefits that extend far beyond basic insulation performance. The primary advantage lies in their exceptional thermal resistance properties, with R-values typically ranging from 6.0 to 7.0 per inch of thickness. This remarkable insulating capacity means that a 3-inch application of closed cell foam provides equivalent thermal protection to 6-8 inches of traditional fiberglass insulation, allowing for more efficient use of wall and roof cavity space.
The superior air sealing properties of closed cell spray foam kits create an effective barrier against unwanted air infiltration, which can account for 25-40% of heating and cooling energy losses in typical homes. Unlike traditional insulation materials that can shift, settle, or leave gaps over time, closed cell foam maintains its integrity and sealing properties for decades. This long-term performance translates to consistent energy savings and improved comfort throughout the building’s lifespan.
Moisture control represents another significant advantage of closed cell spray foam kits. The closed-cell structure creates an impermeable barrier with a vapor permeance rating of less than 1.0 perm, effectively preventing moisture infiltration that can lead to mold growth, wood rot, and structural damage. This moisture barrier functionality is particularly valuable in humid climates, basement applications, and areas prone to condensation issues.
Structural Benefits and Added Value
The rigid nature of cured closed cell foam provides measurable structural reinforcement to building components. Studies have shown that closed cell spray foam kits can increase wall strength by 200-300% when applied to standard wood frame construction. This added structural capacity can be particularly beneficial in high-wind areas, seismic zones, or applications where enhanced building integrity is desired.
Environmental advantages of closed cell spray foam kits include their contribution to reduced energy consumption and lower carbon footprint. The exceptional insulating properties mean heating and cooling systems operate more efficiently, reducing overall energy demand. Many modern formulations use more environmentally friendly blowing agents with lower global warming potential compared to older foam technologies.
The longevity of closed cell foam applications makes these kits an excellent long-term investment. Unlike traditional insulation materials that may require replacement every 15-20 years, properly installed closed cell foam can maintain its performance characteristics for 50+ years. This durability factor, combined with energy savings, often results in a return on investment within 3-5 years of installation.
Top Features to Look for in Closed Cell Spray Foam Kits
When selecting closed cell spray foam kits, several critical features distinguish professional-grade products from basic consumer options. The yield capacity represents one of the most important specifications, indicating the total board feet of foam the kit can produce. Professional kits typically range from 200 to 600 board feet, with larger capacities offering better value for extensive projects. Understanding board foot calculations is essential: one board foot equals one square foot of surface covered at one-inch thickness.
Temperature operating range significantly impacts the performance and usability of closed cell spray foam kits. Premium kits function effectively in temperatures ranging from 60°F to 90°F, with some specialized formulations extending this range to 40°F-100°F. Temperature affects both the chemical reaction rate and the final foam properties, making this specification crucial for seasonal applications or extreme climate conditions.
The pressure rating and mixing ratio accuracy of the application equipment directly influence the quality of the final foam product. Professional-grade closed cell spray foam kits maintain consistent 1:1 mixing ratios under pressures exceeding 1,000 PSI, ensuring proper chemical reaction and optimal foam expansion. Inadequate pressure or incorrect mixing ratios can result in poor adhesion, reduced R-value, and compromised long-term performance.
Advanced Kit Features and Specifications
Spray pattern control and application precision separate high-quality kits from basic alternatives. Advanced spray guns offer adjustable spray patterns from narrow pencil streams for crack filling to wide fan patterns for large surface coverage. The ability to control application thickness and pattern ensures efficient material usage and professional-quality results across different project requirements.
Chemical shelf life and storage requirements become critical factors for contractors and homeowners planning multiple projects. Premium closed cell spray foam kits feature enhanced chemical stability with shelf lives extending 12-18 months when stored properly. Temperature-stable formulations reduce sensitivity to storage conditions, maintaining consistent performance even after extended storage periods.
Safety integration and user protection features distinguish professional kits from consumer products. Comprehensive safety packages include:
- Full-face respirators with appropriate cartridge filtration
- Chemical-resistant coveralls with sealed seams
- Nitrile gloves rated for chemical exposure
- Ventilation guidelines and air quality monitoring recommendations
- Emergency response procedures and first aid protocols
Cleanup and maintenance considerations significantly impact the overall user experience. Quality kits include specialized cleaning solvents, equipment maintenance procedures, and component replacement availability. The ease of equipment cleanup and maintenance directly affects the kit’s long-term value and usability for multiple projects.
Installation Process and Best Practices
Proper installation of closed cell spray foam kits requires meticulous preparation and adherence to manufacturer specifications to achieve optimal results. The installation process begins with comprehensive site preparation, including surface cleaning, temperature verification, and ventilation setup. Substrate preparation is crucial because closed cell foam bonds permanently to most surfaces, making proper preparation essential for long-term performance and easy removal if necessary.
Surface preparation involves removing loose debris, oil, grease, and any materials that might interfere with proper adhesion. Porous surfaces may require priming or sealing to prevent foam from penetrating beyond the intended application area. Metal surfaces should be cleaned with appropriate solvents, while wood surfaces must be dry and free from dust or sawdust. The substrate temperature must be within the kit’s specified range, typically 60-90°F, to ensure proper chemical reaction and foam expansion.
Environmental conditions play a critical role in the success of closed cell spray foam applications. Humidity levels should be below 85% to prevent interference with the chemical reaction process. Wind conditions must be minimal to prevent spray drift and ensure accurate application. Temperature stability throughout the application process is essential, as temperature fluctuations can affect foam expansion rates and final density.
Step-by-Step Application Process
Equipment setup begins with thorough inspection of all components, including hoses, spray guns, and chemical containers. Closed cell spray foam kits require specific pressure settings and mixing ratios, typically maintained through factory-preset equipment. The spray gun should be tested with a brief application to verify proper mixing and spray pattern before beginning the main application.
Application technique involves maintaining consistent spray distance (typically 18-24 inches), steady movement speed, and proper spray angles. The foam should be applied in multiple thin lifts rather than single thick applications, with each lift approximately 1-2 inches thick. This technique ensures proper chemical reaction, optimal cell structure, and prevents overheating that can degrade foam properties.
Quality control during application includes monitoring foam expansion, checking for proper adhesion, and verifying coverage uniformity. Properly applied closed cell spray foam kits exhibit consistent color, smooth surface texture, and complete coverage without voids or thin spots. The foam should expand to approximately 30-40 times its liquid volume within 30-60 seconds of application.
Safety protocols must be rigorously followed throughout the installation process:
- Respiratory protection using appropriate respirators
- Skin protection with chemical-resistant clothing
- Eye protection with safety glasses or face shields
- Ventilation maintenance to prevent vapor accumulation
- Emergency procedures readily available and understood
Cost Analysis and ROI of Closed Cell Spray Foam Kits
The financial benefits of closed cell spray foam kits extend far beyond the initial purchase price, creating substantial long-term value through energy savings, durability, and performance consistency. Initial kit costs typically range from $1,500 to $4,000 depending on coverage capacity and included features, representing a significant cost advantage over professional installation services that often charge $3-7 per square foot for equivalent coverage.
Energy savings from closed cell foam applications frequently exceed 30-50% of heating and cooling costs, depending on the building’s previous insulation levels and local climate conditions. In moderate climates, homeowners report annual savings of $800-1,500 on energy bills, while extreme climate regions can see savings exceeding $2,000 annually. These savings compound over time, often resulting in complete cost recovery within 3-5 years of installation.
The durability factor significantly impacts the long-term value proposition of closed cell spray foam kits. While traditional insulation materials may require replacement or supplementation every 15-20 years, properly installed closed cell foam maintains its performance characteristics for 50+ years. This longevity eliminates recurring insulation costs and provides consistent energy savings throughout the building’s lifespan.
Comprehensive Cost Breakdown
Cost Factor | Initial Investment | Annual Savings | 10-Year Value |
---|---|---|---|
Kit Cost | $2,500-$3,500 | – | – |
Energy Savings | – | $1,200-$2,000 | $12,000-$20,000 |
Maintenance Avoided | – | $200-$400 | $2,000-$4,000 |
Property Value Increase | – | – | $8,000-$15,000 |
Professional installation comparison reveals substantial cost advantages for DIY applications using closed cell spray foam kits. Professional spray foam installation typically costs $4-8 per square foot, while DIY kits reduce this cost to $1.50-$3.00 per square foot, including all materials and safety equipment. For typical residential applications covering 1,000-2,000 square feet, this represents savings of $2,500-$10,000 compared to professional installation.
Property value enhancement represents an additional financial benefit of closed cell foam applications. Energy-efficient homes with superior insulation systems command premium prices in real estate markets, with efficiency upgrades often returning 70-90% of their cost in increased property value. The permanent nature of closed cell foam makes it particularly attractive to potential buyers concerned about long-term energy costs.
Tax incentives and rebates can further improve the financial attractiveness of closed cell spray foam kits. Many jurisdictions offer energy efficiency tax credits, utility rebates, or financing programs that reduce the effective cost of insulation improvements. These incentives, combined with energy savings, can result in net-positive returns within the first year of installation.
Common Applications and Use Cases
Closed cell spray foam kits excel in a diverse range of applications where superior insulation performance, air sealing, and moisture control are priorities. Residential applications represent the largest market segment, with homeowners using these kits for basement insulation, crawl space encapsulation, attic air sealing, and rim joist insulation. The versatility of spray foam allows for effective treatment of irregular surfaces, tight spaces, and complex geometries that challenge traditional insulation materials.
Basement and crawl space applications benefit tremendously from the moisture barrier properties of closed cell foam. These below-grade environments often experience humidity issues, temperature fluctuations, and air infiltration that compromise comfort and energy efficiency. Closed cell spray foam kits create a complete thermal and moisture barrier that prevents condensation, reduces humidity levels, and eliminates cold spots that can lead to mold growth and structural damage.
Attic and roof applications leverage the superior R-value and air sealing properties of closed cell foam to create high-performance thermal barriers. The ability to spray foam directly to roof decking creates a conditioned attic space that protects HVAC equipment and ductwork from temperature extremes. This application approach can reduce cooling costs by 15-25% in hot climates while preventing ice dam formation in cold regions.
Specialized Commercial Applications
Metal building insulation represents a significant opportunity for closed cell spray foam kits, particularly in agricultural, industrial, and commercial structures. Metal buildings are notorious for condensation problems, thermal bridging, and air infiltration issues that spray foam effectively addresses. The structural reinforcement provided by closed cell foam also helps reduce panel deflection and noise transmission in metal building applications.
Pole barn and agricultural applications benefit from the moisture control and pest resistance properties of closed cell foam. These structures often house valuable equipment, feed supplies, or livestock that require protection from moisture and temperature extremes. Closed cell spray foam kits provide an effective solution for creating controlled environments while preventing pest infiltration and moisture damage.
Marine and RV applications take advantage of the lightweight, moisture-resistant properties of closed cell foam for specialized insulation needs. The ability to conform to irregular surfaces and provide excellent thermal performance in thin sections makes these kits ideal for space-constrained applications where traditional insulation would be impractical.
For projects requiring roofing applications, spray foam roofing provides additional specialized solutions for commercial and residential flat roof systems.
Renovation and Retrofit Projects
Historic building preservation often requires insulation solutions that work with existing structures without compromising architectural integrity. Closed cell spray foam kits can be applied to irregular surfaces, cavity spaces, and hard-to-reach areas that would be difficult or impossible to insulate with traditional materials. The ability to add insulation without major structural modifications makes these kits valuable for historic renovation projects.
Energy efficiency upgrades in existing buildings frequently involve addressing air leakage and thermal bridging issues that spray foam effectively solves. Retrofit applications can achieve dramatic energy savings by sealing air leaks around windows, doors, electrical penetrations, and other common problem areas. The ability to apply foam from the interior without exterior wall modifications makes these upgrades practical and cost-effective.
Soundproofing applications benefit from the dense, rigid structure of closed cell foam, which provides excellent sound dampening properties. Recording studios, home theaters, and noise-sensitive environments can use closed cell spray foam kits to create effective acoustic barriers while simultaneously improving thermal performance.
Safety Considerations and Precautions
Working with closed cell spray foam kits requires comprehensive safety protocols to protect applicators and building occupants from potential health hazards associated with chemical exposure and application processes. The chemical components in these kits contain isocyanates and other reactive compounds that can cause serious health effects if proper safety measures are not followed. Understanding and implementing appropriate safety procedures is essential for successful and safe foam application.
Respiratory protection represents the most critical safety requirement when using closed cell spray foam kits. The chemical reaction process releases vapors and aerosols that can cause respiratory irritation, sensitization, and long-term health effects. Professional-grade respirators with appropriate cartridge filtration are mandatory, not optional equipment. Half-face respirators provide minimum protection, while full-face respirators offer superior protection for extended applications.
Skin contact prevention requires comprehensive protective clothing including chemical-resistant coveralls, nitrile gloves, and protective footwear. Direct skin contact with uncured foam chemicals can cause chemical burns, sensitization reactions, and permanent skin damage. All protective equipment must be properly fitted and inspected before each use, with damaged equipment replaced immediately.
Ventilation and Air Quality Management
Adequate ventilation is essential throughout the application process and for 24-48 hours after foam application. Mechanical ventilation systems should provide at least 1 air change per hour during application and continue until foam curing is complete. Natural ventilation through open windows and doors may be insufficient for safe chemical vapor removal, particularly in enclosed spaces.
Air quality monitoring helps ensure safe working conditions and proper ventilation effectiveness. Volatile organic compound (VOC) monitors can detect potentially dangerous vapor concentrations, while oxygen monitors ensure adequate air quality in enclosed spaces. Professional applications often employ continuous air monitoring to verify safe working conditions throughout the project.
Occupancy restrictions must be strictly enforced during and after foam application. Building occupants, particularly children, pregnant women, and individuals with respiratory conditions, should remain away from application areas for 24-48 hours or until proper ventilation has been verified. Pet safety also requires similar precautions, as animals may be more sensitive to chemical vapors.
Emergency Response Procedures
Chemical exposure protocols must be established before beginning any closed cell spray foam kit application. Eye wash stations, emergency shower facilities, and appropriate first aid supplies should be readily available. All applicators must understand proper response procedures for skin contact, eye contact, and inhalation exposure incidents.
Fire safety considerations include understanding the flammability characteristics of both uncured and cured foam materials. Uncured foam chemicals are flammable and require appropriate fire suppression equipment nearby. Cured foam is combustible and may require flame retardant treatments in certain applications to meet building code requirements.
Waste disposal of unused chemicals, contaminated equipment, and protective materials requires compliance with local environmental regulations. Many foam chemicals are considered hazardous waste and cannot be disposed of in regular trash or poured down drains. Professional waste disposal services may be required for proper chemical disposal.
Training and certification programs are available through manufacturers and industry organizations to ensure proper application techniques and safety procedures. These programs cover chemical handling, equipment operation, safety protocols, and troubleshooting common application problems. Certification demonstrates commitment to safe, professional application practices.
Maintenance and Longevity
Closed cell spray foam kits create insulation systems that require minimal maintenance while providing decades of consistent performance when properly installed and protected. The closed-cell structure and chemical stability of cured foam resist degradation from temperature cycling, moisture exposure, and normal building settling. However, understanding proper maintenance practices and potential issues helps ensure optimal long-term performance and return on investment.
Regular inspection protocols should include visual examination of exposed foam surfaces for signs of damage, discoloration, or degradation. Properly cured closed cell foam maintains its light yellow to tan color and rigid texture indefinitely under normal conditions. Dark discoloration, soft spots, or cracking may indicate moisture infiltration, chemical degradation, or installation problems requiring professional evaluation.
UV protection is essential for any closed cell foam exposed to direct sunlight, as ultraviolet radiation can cause surface degradation and color changes. Foam applications in attics, crawl spaces, or exterior locations should be protected with appropriate coverings or coatings. Acrylic or polyurethane protective coatings can extend the life of exposed foam surfaces while maintaining thermal performance.
Long-Term Performance Monitoring
Thermal performance monitoring helps verify that closed cell spray foam kits continue delivering expected energy savings over time. Annual energy usage tracking can identify potential performance degradation or building envelope issues that may require attention. Significant changes in energy consumption patterns may indicate air leakage, thermal bridging, or foam degradation requiring investigation.
Moisture monitoring in foam-treated areas helps prevent conditions that could compromise long-term performance. While closed cell foam provides excellent moisture protection, building envelope failures, plumbing leaks, or roof damage can introduce moisture that affects foam integrity. Regular moisture monitoring using electronic moisture meters or visual inspection helps identify problems before they become serious issues.
Structural integrity of foam-treated building components should be monitored as part of routine building maintenance. The structural reinforcement provided by closed cell foam helps buildings resist wind loads, seismic forces, and normal settling. However, extreme weather events or structural damage may require professional evaluation to ensure continued performance.
Repair and Modification Procedures
Damage repair of closed cell foam applications requires careful assessment and appropriate repair techniques. Small areas of damaged foam can often be repaired using small spray foam kits or foam-compatible sealants. Larger damaged areas may require professional repair or replacement to maintain thermal performance and structural integrity.
Modification requirements for electrical, plumbing, or HVAC installations in foam-treated areas require special considerations. Closed cell foam bonds permanently to most surfaces and cannot be easily removed without damaging surrounding materials. Planning for future modifications during initial installation helps avoid costly removal and replacement procedures.
Compatibility with building modifications should be considered when planning renovations or additions to foam-treated buildings. The exceptional air sealing properties of closed cell foam may affect building ventilation requirements, moisture management, and indoor air quality. Professional consultation may be necessary to ensure building modifications maintain proper performance and safety.
Frequently Asked Questions About Closed Cell Spray Foam Kits
What is the coverage area of typical closed cell spray foam kits?
Closed cell spray foam kits typically provide coverage ranging from 200 to 600 board feet, depending on the kit size and manufacturer specifications. One board foot equals one square foot of surface covered at one-inch thickness. For example, a 600 board foot kit can cover 600 square feet at 1-inch thickness, 300 square feet at 2-inch thickness, or 200 square feet at 3-inch thickness. The actual coverage depends on application thickness, surface conditions, and applicator technique.
How long does it take for closed cell spray foam to cure completely?
Closed cell spray foam kits typically achieve surface cure within 30-60 seconds of application, becoming tack-free and walkable within 1-2 minutes. However, complete chemical cure requires 24-48 hours depending on temperature, humidity, and foam thickness. During the curing process, the foam continues to develop full strength and thermal properties. Areas should remain undisturbed during the curing period to ensure optimal performance.
Can closed cell spray foam kits be used in cold weather conditions?
Most closed cell spray foam kits require substrate temperatures between 60-90°F for proper application and curing. Cold weather applications below 60°F can result in poor foam expansion, inadequate adhesion, and compromised thermal properties. Some manufacturers offer cold-weather formulations that function down to 40°F, but these require specialized equipment and techniques. Indoor applications in heated spaces typically maintain adequate temperatures year-round.
What safety equipment is required when using closed cell spray foam kits?
Closed cell spray foam kits require comprehensive safety equipment including full-face respirators with appropriate cartridge filtration, chemical-resistant coveralls, nitrile gloves, and protective footwear. Adequate ventilation is essential throughout application and curing. Eye protection, first aid supplies, and emergency response procedures must be available. All safety equipment should be properly fitted and inspected before each use.
How do closed cell spray foam kits compare to professional installation costs?
Closed cell spray foam kits typically cost $1.50-$3.00 per square foot for DIY applications, while professional installation ranges from $4-8 per square foot. For typical residential applications covering 1,000-2,000 square feet, DIY kits can save $2,500-$10,000 compared to professional installation. However, professional installation may be required for complex applications, building code compliance, or warranty requirements.
What maintenance is required for closed cell spray foam applications?
Closed cell spray foam kits create low-maintenance insulation systems requiring only periodic visual inspection for damage or degradation. Properly installed foam should maintain its appearance and performance for 50+ years without maintenance. UV protection is required for exposed foam surfaces, and any physical damage should be repaired promptly to maintain thermal performance and air sealing properties.
Are there any building code restrictions for closed cell spray foam applications?
Closed cell spray foam kits must comply with local building codes regarding fire resistance, vapor barriers, and ventilation requirements. Some jurisdictions require professional installation for certain applications or building types. Flame spread and smoke development ratings may require protective coatings or barriers in occupied spaces. Always consult local building officials before beginning spray foam applications to ensure code compliance.
Can closed cell spray foam kits be applied over existing insulation?
Closed cell spray foam kits can often be applied over existing insulation materials, but compatibility and performance must be carefully considered. The foam bonds permanently to most surfaces and cannot be easily removed. Existing insulation should be clean, dry, and free from moisture problems. In some cases, removing existing insulation may be necessary to achieve optimal performance and identify hidden problems.
Ready to transform your building’s energy efficiency with superior insulation performance? Closed cell spray foam kits offer the perfect combination of professional-grade results and DIY convenience. Visit our complete selection of closed cell spray foam kits to find the perfect solution for your project needs and start saving on energy costs today.