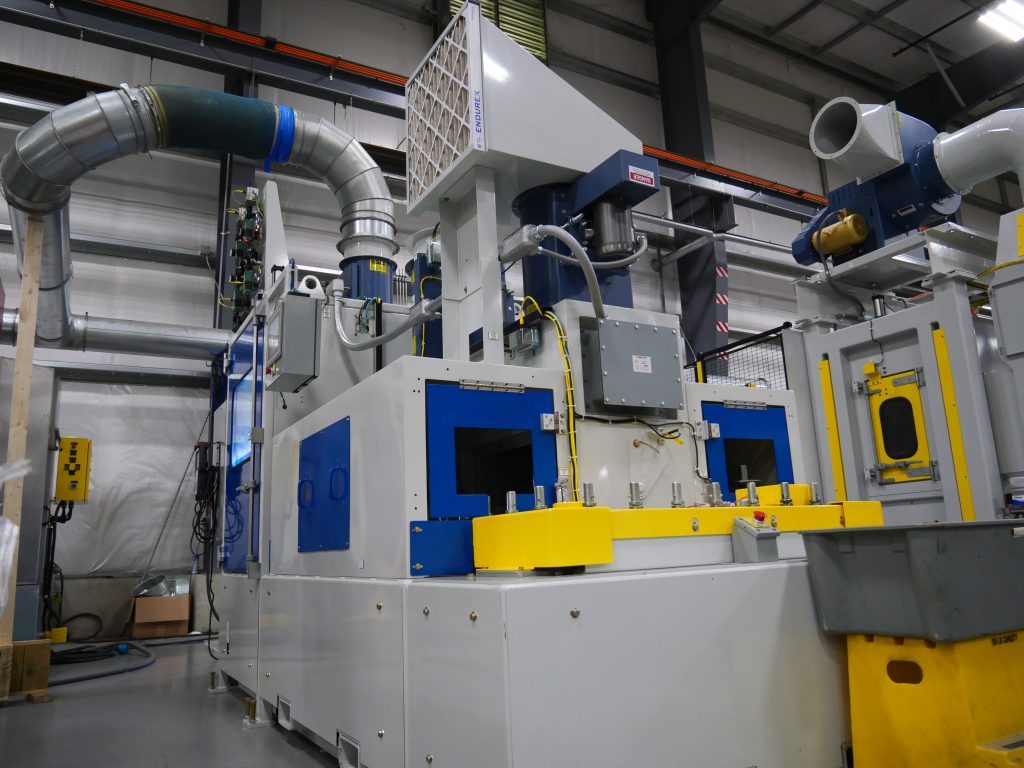
The manufacturing industry has undergone a revolutionary transformation with the advent of automatic spray painting systems. These sophisticated technologies have fundamentally changed how businesses approach surface coating, offering unprecedented levels of precision, efficiency, and quality control that manual painting methods simply cannot match. From automotive assembly lines to furniture production facilities, automatic spray painting has become the cornerstone of modern manufacturing operations, delivering consistent results while significantly reducing labor costs and material waste.
What is Automatic Spray Painting?
Automatic spray painting represents a cutting-edge industrial process that utilizes computer-controlled systems to apply coatings, paints, and finishes to various surfaces without human intervention. Unlike traditional manual painting methods, these systems employ robotic arms, programmable logic controllers (PLC), and sophisticated sensors to ensure uniform application across complex geometries and surfaces. The technology combines precision engineering with advanced software algorithms to deliver consistent coating thickness, optimal coverage patterns, and superior finish quality.
The core components of an automatic spray painting system include robotic manipulators, spray guns, paint delivery systems, environmental controls, and safety mechanisms. These elements work in perfect harmony to create a seamless coating process that can operate continuously for extended periods, dramatically increasing production capacity while maintaining exceptional quality standards. The integration of artificial intelligence and machine learning algorithms has further enhanced these systems, enabling predictive maintenance, real-time quality monitoring, and adaptive coating parameters based on environmental conditions.
Modern automatic spray painting systems can handle a wide variety of coating materials, from traditional solvent-based paints to advanced water-based formulations, powder coatings, and specialized protective finishes. The versatility of these systems makes them suitable for diverse applications across multiple industries, including automotive, aerospace, electronics, furniture, and construction equipment manufacturing.
Key Benefits of Automatic Spray Painting Systems
Enhanced Quality Control and Consistency
One of the most significant advantages of automatic spray painting technology is its ability to deliver unparalleled consistency in coating application. Unlike manual painting, which is subject to human variables such as fatigue, skill level, and environmental factors, automated systems maintain precise control over spray patterns, coating thickness, and application speed. This consistency translates to superior finish quality, reduced defect rates, and improved overall product aesthetics.
The precision offered by automatic spray painting systems is particularly evident in their ability to maintain optimal coating thickness across complex geometries. Advanced sensors continuously monitor the coating process, making real-time adjustments to spray parameters to ensure uniform coverage even on intricate surfaces with varying contours, angles, and accessibility challenges. This level of precision is virtually impossible to achieve with manual painting methods, making automation essential for industries requiring strict quality standards.
Significant Cost Reduction and Efficiency Gains
Implementing automatic spray painting systems delivers substantial cost savings through multiple channels. Labor costs, which typically represent 40-60% of total painting expenses, are dramatically reduced as fewer operators are required to oversee the automated process. Additionally, material waste is minimized through precise application control, reducing overspray and ensuring optimal paint utilization rates that can exceed 90% efficiency.
The speed of automatic spray painting systems far surpasses manual methods, with production rates increasing by 200-400% in many applications. This increased throughput allows manufacturers to meet growing demand without proportional increases in labor or facility requirements. The consistent operating speed also enables better production planning and scheduling, improving overall manufacturing efficiency and reducing bottlenecks in the production process.
Improved Safety and Environmental Benefits
Automatic spray painting systems significantly enhance workplace safety by reducing human exposure to hazardous chemicals, volatile organic compounds (VOCs), and potentially harmful spray particles. Operators work in controlled environments away from direct contact with coating materials, substantially reducing health risks associated with prolonged exposure to industrial paints and solvents.
Environmental benefits of automatic spray painting include reduced material waste, lower VOC emissions, and improved energy efficiency. The precision of automated systems minimizes overspray, reducing air pollution and material consumption. Many modern systems incorporate closed-loop recycling capabilities, further reducing environmental impact while lowering operational costs.
Types of Automatic Spray Painting Systems
Robotic Spray Painting Systems
Robotic automatic spray painting systems represent the pinnacle of coating technology, utilizing articulated robotic arms equipped with sophisticated spray guns and advanced control systems. These systems offer exceptional flexibility, capable of programming complex movement patterns to accommodate diverse product geometries and coating requirements. The six-axis movement capability of industrial robots enables access to challenging angles and surfaces that would be difficult or impossible to reach with manual painting methods.
The programming flexibility of robotic automatic spray painting systems allows for easy adaptation to different products and coating specifications. Recipe-based programming enables quick changeovers between different paint formulations, spray patterns, and application parameters, making these systems ideal for manufacturers producing diverse product lines with varying coating requirements.
Reciprocating Spray Systems
Reciprocating automatic spray painting systems utilize linear movement mechanisms to apply coatings to flat or cylindrical surfaces. These systems are particularly effective for high-volume production of similar items, such as panels, doors, or cylindrical components. The reciprocating motion ensures uniform coverage while maintaining consistent application speed and coating thickness.
The simplicity of reciprocating systems makes them cost-effective solutions for manufacturers with specific coating requirements. While less flexible than robotic systems, they offer excellent value for applications requiring consistent, high-quality coating of similar products. The linear motion control is highly precise, enabling tight tolerances and exceptional finish quality.
Disc and Bell Spray Systems
Disc and bell automatic spray painting systems employ rotating atomization devices to create fine paint particles for superior finish quality. These systems are particularly effective for automotive applications and high-end finishing requirements where surface smoothness and appearance are critical. The centrifugal force generated by rotating discs or bells creates extremely fine paint particles that result in smooth, even coatings with minimal orange peel texture.
The efficiency of disc and bell systems is exceptional, with transfer efficiency rates often exceeding 85%. This high efficiency reduces material consumption and minimizes overspray, making these systems environmentally friendly and cost-effective for high-volume production applications.
Industries Benefiting from Automatic Spray Painting
Automotive Manufacturing
The automotive industry has been at the forefront of automatic spray painting adoption, with virtually every major manufacturer utilizing automated coating systems for vehicle production. The demanding quality standards, high production volumes, and complex geometries of automotive components make automated painting systems essential for competitive manufacturing. From primer application to topcoat finishing, automatic spray painting ensures consistent color matching, uniform coverage, and superior durability.
Modern automotive automatic spray painting systems incorporate advanced technologies such as color-changing capabilities, allowing single paint lines to handle multiple colors without contamination. This flexibility enables just-in-time manufacturing and reduces inventory requirements while maintaining production efficiency. The integration of quality control sensors ensures that every painted component meets strict automotive standards before proceeding to assembly.
Aerospace and Defense
The aerospace industry relies heavily on automatic spray painting systems for applying specialized coatings that must meet stringent performance requirements. Aircraft components require precise coating thickness for weight control, corrosion resistance, and aerodynamic performance. The repeatability and precision of automated systems ensure compliance with strict aerospace standards while reducing the risk of human error in critical applications.
Automatic spray painting systems in aerospace applications often incorporate advanced material handling capabilities to accommodate large, complex components such as fuselage sections, wing panels, and engine components. The ability to program precise coating patterns ensures uniform protection while minimizing weight penalties associated with excess coating material.
Electronics and Consumer Goods
The electronics industry utilizes automatic spray painting for applying protective coatings, decorative finishes, and functional coatings to circuit boards, housings, and components. The precision required for electronic applications, combined with the need for contamination-free environments, makes automated systems essential for maintaining product quality and reliability.
Consumer goods manufacturers benefit from automatic spray painting systems’ ability to deliver consistent aesthetic finishes across large production volumes. From appliances to furniture, automated coating systems ensure color consistency, finish quality, and production efficiency that manual methods cannot match.
Technology Integration and Smart Manufacturing
IoT and Industry 4.0 Integration
Modern automatic spray painting systems are increasingly integrated with Internet of Things (IoT) technologies and Industry 4.0 principles. These smart systems collect real-time data on coating parameters, material consumption, environmental conditions, and system performance. This data enables predictive maintenance, quality optimization, and production efficiency improvements through advanced analytics and machine learning algorithms.
The connectivity of automatic spray painting systems allows for remote monitoring, diagnostics, and optimization, reducing downtime and improving overall equipment effectiveness (OEE). Integration with enterprise resource planning (ERP) systems enables seamless coordination between coating operations and broader manufacturing processes.
Advanced Control Systems
The control systems powering automatic spray painting technology have evolved significantly, incorporating artificial intelligence, machine learning, and advanced sensor technologies. These systems can automatically adjust spray parameters based on real-time feedback, environmental conditions, and product specifications. The result is consistently optimal coating quality with minimal human intervention.
Vision systems integrated with automatic spray painting equipment provide real-time quality monitoring, detecting defects, coating thickness variations, and coverage issues immediately. This instant feedback enables immediate corrections and prevents defective products from advancing through the production process.
Cost Analysis and Return on Investment
Initial Investment Considerations
The initial investment in automatic spray painting systems varies significantly based on system complexity, production requirements, and specific application needs. Basic reciprocating systems may require investments starting around $50,000-$100,000, while comprehensive robotic systems can range from $200,000 to over $1 million for fully integrated installations.
Investment Breakdown:
- Robotic Systems: $200,000 – $1,000,000+
- Reciprocating Systems: $50,000 – $200,000
- Disc/Bell Systems: $100,000 – $500,000
- Installation and Integration: 20-30% of equipment cost
- Training and Startup: 5-10% of total investment
Operating Cost Savings
The operational savings from automatic spray painting systems typically provide return on investment within 18-36 months, depending on production volume and application requirements. Labor cost reductions often represent the largest savings component, with single automated systems potentially replacing 2-6 manual painters while operating continuously.
Annual Savings Potential:
- Labor Costs: $150,000 – $400,000 per system
- Material Savings: 15-30% reduction in paint consumption
- Reduced Rework: 50-80% decrease in defect rates
- Increased Throughput: 200-400% production increase
- Energy Efficiency: 20-40% reduction in energy consumption
Long-term Financial Benefits
Beyond immediate operational savings, automatic spray painting systems provide long-term financial benefits through improved product quality, reduced liability, and enhanced competitiveness. The consistency and quality of automated coating processes often enable premium pricing and improved customer satisfaction, leading to increased market share and profitability.
The scalability of automatic spray painting systems allows manufacturers to expand production capacity without proportional increases in labor or facility requirements. This scalability becomes particularly valuable during periods of market growth or when entering new product categories.
Maintenance and Support Requirements
Preventive Maintenance Programs
Successful automatic spray painting operations require comprehensive preventive maintenance programs to ensure optimal performance and longevity. Regular maintenance schedules should include cleaning spray guns, replacing wear parts, calibrating sensors, and updating software systems. The complexity of automated systems necessitates skilled technicians and specialized maintenance procedures.
Key Maintenance Activities:
- Daily: System inspection, cleaning, basic calibration
- Weekly: Filter replacement, sensor calibration, system backup
- Monthly: Comprehensive system analysis, wear part inspection
- Quarterly: Software updates, major component inspection
- Annually: Complete system overhaul, certification renewal
Technical Support and Training
Effective operation of automatic spray painting systems requires ongoing technical support and comprehensive training programs. Manufacturers should establish relationships with equipment suppliers that provide responsive technical support, spare parts availability, and continuous training opportunities for operators and maintenance personnel.
The investment in proper training often determines the success of automatic spray painting implementations. Well-trained operators can maximize system efficiency, minimize downtime, and ensure optimal coating quality. Training programs should cover system operation, troubleshooting, maintenance procedures, and safety protocols.
Future Trends and Innovations
Artificial Intelligence and Machine Learning
The future of automatic spray painting lies in the integration of artificial intelligence and machine learning technologies. These advanced systems will continuously learn from operational data, automatically optimizing coating parameters, predicting maintenance requirements, and adapting to changing production conditions. AI-powered systems will enable predictive quality control, identifying potential issues before they affect production.
Machine learning algorithms will enhance automatic spray painting systems’ ability to handle complex geometries, variable surface conditions, and diverse coating requirements. These systems will automatically adjust spray patterns, material flow rates, and environmental controls based on real-time analysis of coating performance and quality metrics.
Sustainable Coating Technologies
Environmental sustainability is driving innovation in automatic spray painting technology, with new systems designed to minimize environmental impact while maximizing efficiency. Water-based coatings, powder coating systems, and closed-loop recycling technologies are becoming increasingly prevalent in automated coating applications.
Future automatic spray painting systems will incorporate advanced filtration and recovery systems, enabling near-zero waste operations. These systems will capture and recycle overspray materials, reducing environmental impact while lowering operational costs. The integration of renewable energy sources and energy-efficient components will further enhance the sustainability profile of automated coating operations.
Selecting the Right Automatic Spray Painting System
Application Assessment
Selecting the appropriate automatic spray painting system requires thorough analysis of production requirements, product specifications, and operational constraints. Manufacturers must evaluate factors such as production volume, product complexity, coating requirements, and available floor space when choosing between different system types.
Key Selection Criteria:
- Production Volume: Daily/hourly coating requirements
- Product Complexity: Geometry, size, weight considerations
- Coating Requirements: Material types, thickness, finish quality
- Flexibility Needs: Product changeover frequency
- Budget Constraints: Initial investment and operational costs
- Space Requirements: Available floor space and facility layout
Vendor Evaluation
Choosing the right automatic spray painting system supplier is crucial for successful implementation and long-term operation. Manufacturers should evaluate vendors based on technical expertise, industry experience, support capabilities, and financial stability. The selected vendor should provide comprehensive support including system design, installation, training, and ongoing maintenance.
Vendor Evaluation Factors:
- Technical Expertise: Industry knowledge and experience
- Support Network: Local support availability and response times
- Reference Customers: Successful installations in similar applications
- Financial Stability: Long-term viability and support capability
- Training Programs: Comprehensive operator and maintenance training
- Spare Parts Availability: Reliable parts supply and inventory
For manufacturers also considering complementary industrial equipment, belt dressing spray systems can provide additional maintenance solutions for automated production lines.
Implementation Best Practices
Project Planning and Preparation
Successful automatic spray painting implementation requires careful project planning and preparation. Manufacturers should establish clear project objectives, timelines, and success metrics before beginning system installation. Proper planning includes facility preparation, utility requirements, safety considerations, and personnel training schedules.
Implementation Timeline:
- Phase 1: Requirements analysis and system selection (2-4 weeks)
- Phase 2: System design and engineering (4-8 weeks)
- Phase 3: Manufacturing and testing (8-16 weeks)
- Phase 4: Installation and commissioning (2-4 weeks)
- Phase 5: Training and startup (2-4 weeks)
- Phase 6: Production optimization (4-8 weeks)
Performance Monitoring and Optimization
Continuous monitoring and optimization are essential for maximizing the benefits of automatic spray painting systems. Manufacturers should establish key performance indicators (KPIs) and implement regular review processes to identify improvement opportunities. Data collection and analysis enable ongoing optimization of coating parameters, maintenance schedules, and operational procedures.
Key Performance Metrics:
- Coating Quality: Defect rates, finish consistency, thickness uniformity
- Production Efficiency: Throughput rates, uptime percentage, changeover times
- Material Utilization: Transfer efficiency, waste reduction, cost per unit
- Maintenance Performance: Downtime frequency, maintenance costs, parts consumption
- Safety Metrics: Incident rates, exposure levels, compliance scores
Ready to transform your manufacturing operations with cutting-edge automatic spray painting technology? Contact our experts today to discover how automated coating systems can revolutionize your production efficiency, reduce costs, and deliver superior quality results that exceed your customers’ expectations.
Frequently Asked Questions About Automatic Spray Painting
Q: What types of materials can be applied using automatic spray painting systems? A: Automatic spray painting systems can apply a wide variety of materials including solvent-based paints, water-based coatings, powder coatings, primers, topcoats, protective finishes, and specialized industrial coatings. The system configuration determines material compatibility.
Q: How much space is required for an automatic spray painting installation? A: Space requirements for automatic spray painting systems vary significantly based on system type and production requirements. Basic systems may require 500-1000 square feet, while comprehensive robotic installations can require 2000-5000 square feet or more.
Q: What is the typical payback period for automatic spray painting systems? A: Most automatic spray painting systems provide return on investment within 18-36 months, depending on production volume, labor costs, and material savings. High-volume operations often achieve payback in 12-24 months.
Q: Can automatic spray painting systems handle color changes efficiently? A: Yes, modern automatic spray painting systems can accommodate color changes through automated flushing systems, quick-change spray guns, and color-changing technologies. Changeover times typically range from 5-30 minutes depending on system complexity.
Q: What maintenance is required for automatic spray painting systems? A: Automatic spray painting systems require regular maintenance including daily cleaning, weekly filter changes, monthly calibration, and quarterly comprehensive inspections. Proper maintenance ensures optimal performance and longevity.
Q: Are automatic spray painting systems suitable for small manufacturers? A: Automatic spray painting systems are available in various sizes and configurations to suit different production scales. Even small manufacturers can benefit from automated systems designed for lower volume applications.
Q: How do automatic spray painting systems improve safety? A: Automatic spray painting systems enhance safety by reducing human exposure to hazardous chemicals, implementing automated safety controls, providing enclosed operating environments, and minimizing direct contact with coating materials.
Q: What training is required for operating automatic spray painting systems? A: Operating automatic spray painting systems requires comprehensive training covering system operation, safety procedures, maintenance protocols, and troubleshooting techniques. Training duration typically ranges from 1-4 weeks depending on system complexity.